Plattformen plasseres på feltet

Sammenkopling og slep
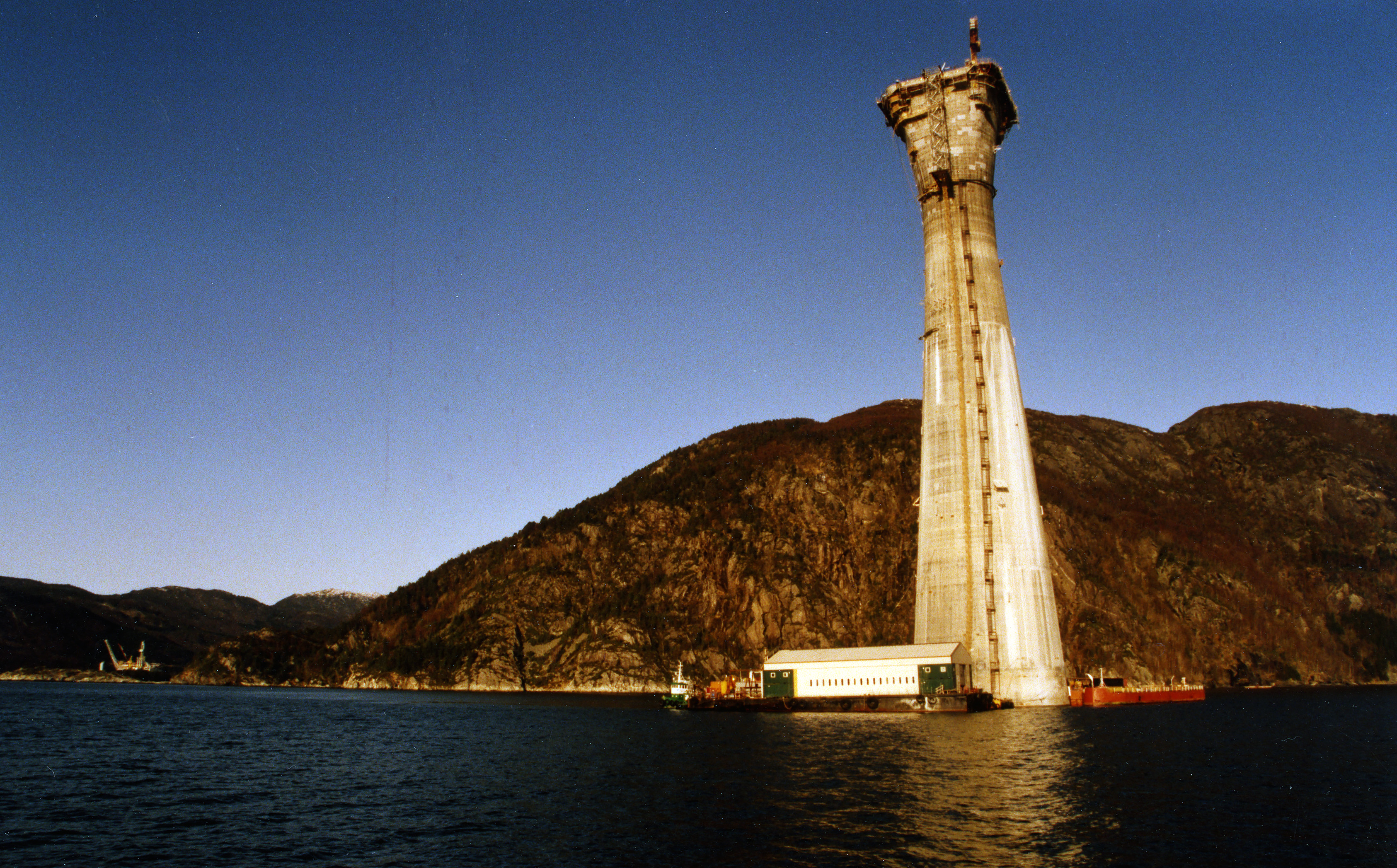
For det første var plattformen den høyeste konstruksjonen i verden som noensinne hadde blitt slept og det var den første bunnfaste plattformen som skulle plasseres nord 62 grader nord noe som også innebar at slepet ble det lengste som var foretatt på norsk kontinentalsokkel.
I mars 1993 ble Condeepen gjort klar til å ta imot dekket som skulle slepes fra Stavanger til Vats. Den 24. mars ble betongkonstruksjonen senket ned slik at det bare var noen få meter av skaftet som var synlig over vannflaten. Det var med stor spenning man fulgte ned operasjonen for minnet om Sleipner-havariet (les artikkel) var ennå ferskt hos de fleste som overvar prøvenedsenkningen. Men alt gikk som planlagt.
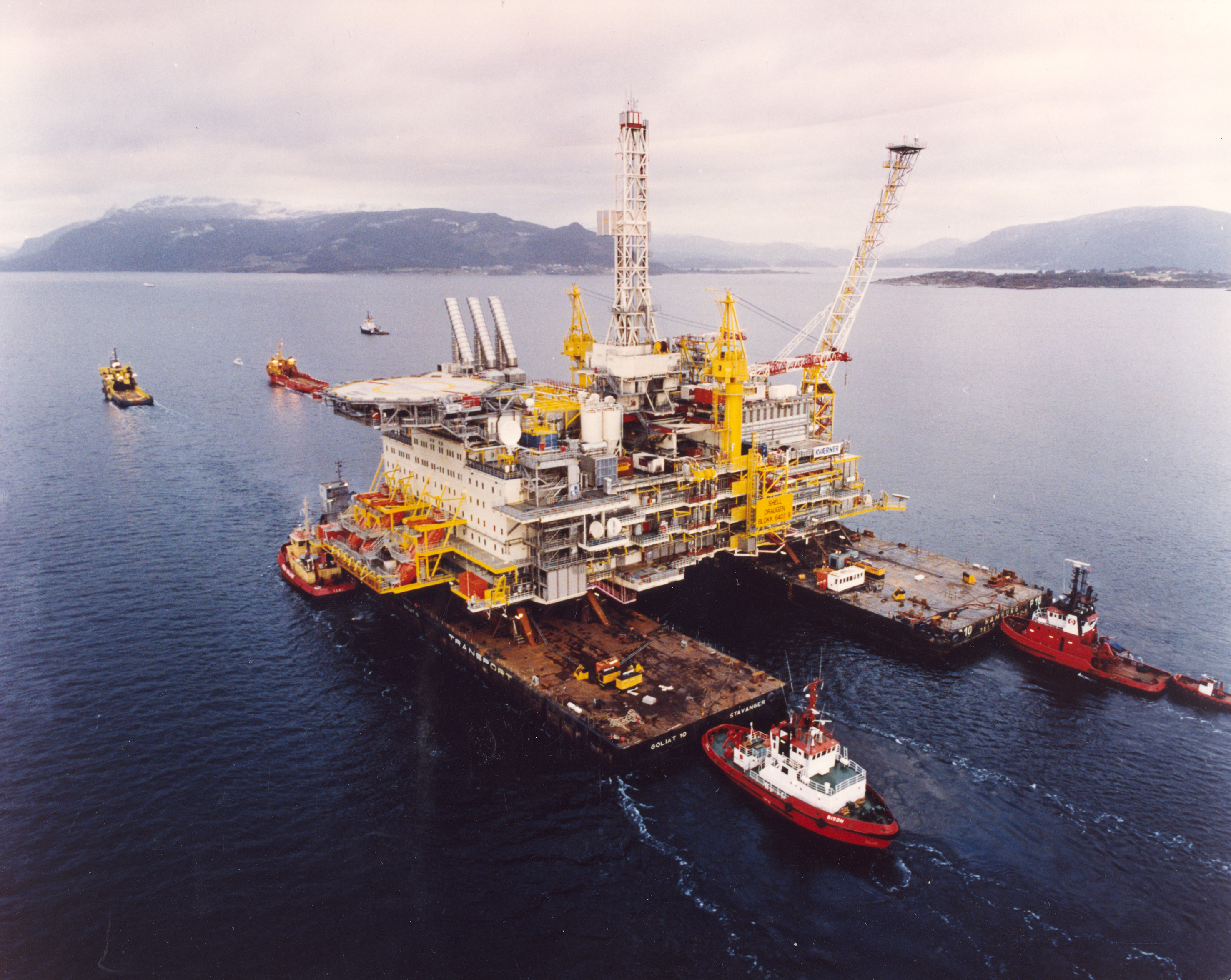
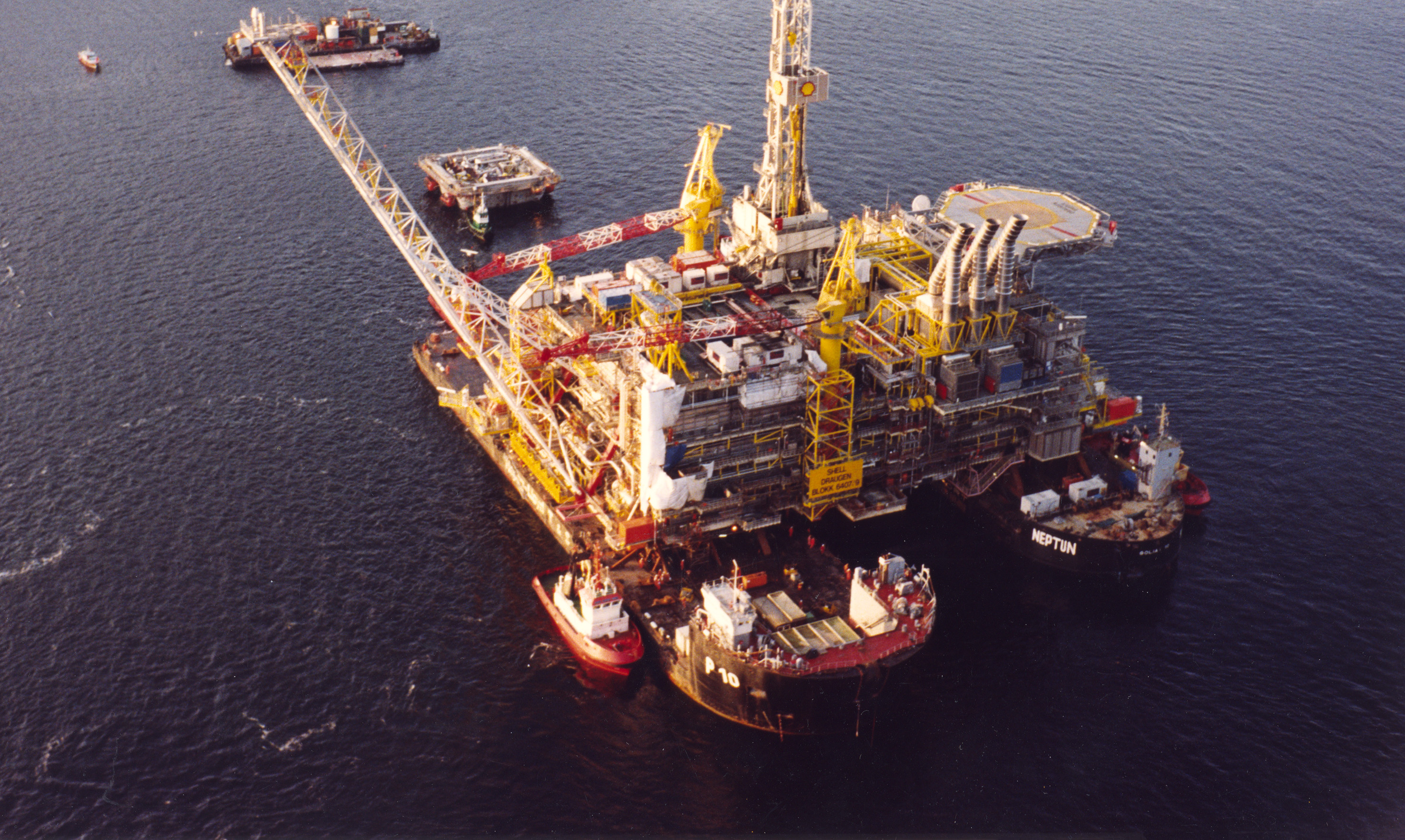
I mellomtiden var dekket gjort ferdig på Rosenberg Verft i Stavanger. 6. mars ble dekket overført til to kjempestore lektere og slept inn i fjorden av fem taubåter. Da dagen for sammenkopling kom ble lekterne med dekket manøvrert på plass over betongskaftet og så begynte hevingen av plattformen. Det tillatte avviket fra ideell plassering av dekket i forhold til dekket var bare 40 millimeter, så det gjaldt å være nøyaktig i alle deler av operasjonen. Etter hvert som man pumpet ut store mengder vann fra lagercellene hevet condeepen seg og overtok vekten fra lekterne og fortsatte å løfte dekket høyt opp over vannet. Sammenkoplingen ble unnagjort helt etter planen og nå stod bare sammenkoplingen av rør og kabelsystemer igjen før plattformen kunne begynne sin ferd mot nord.
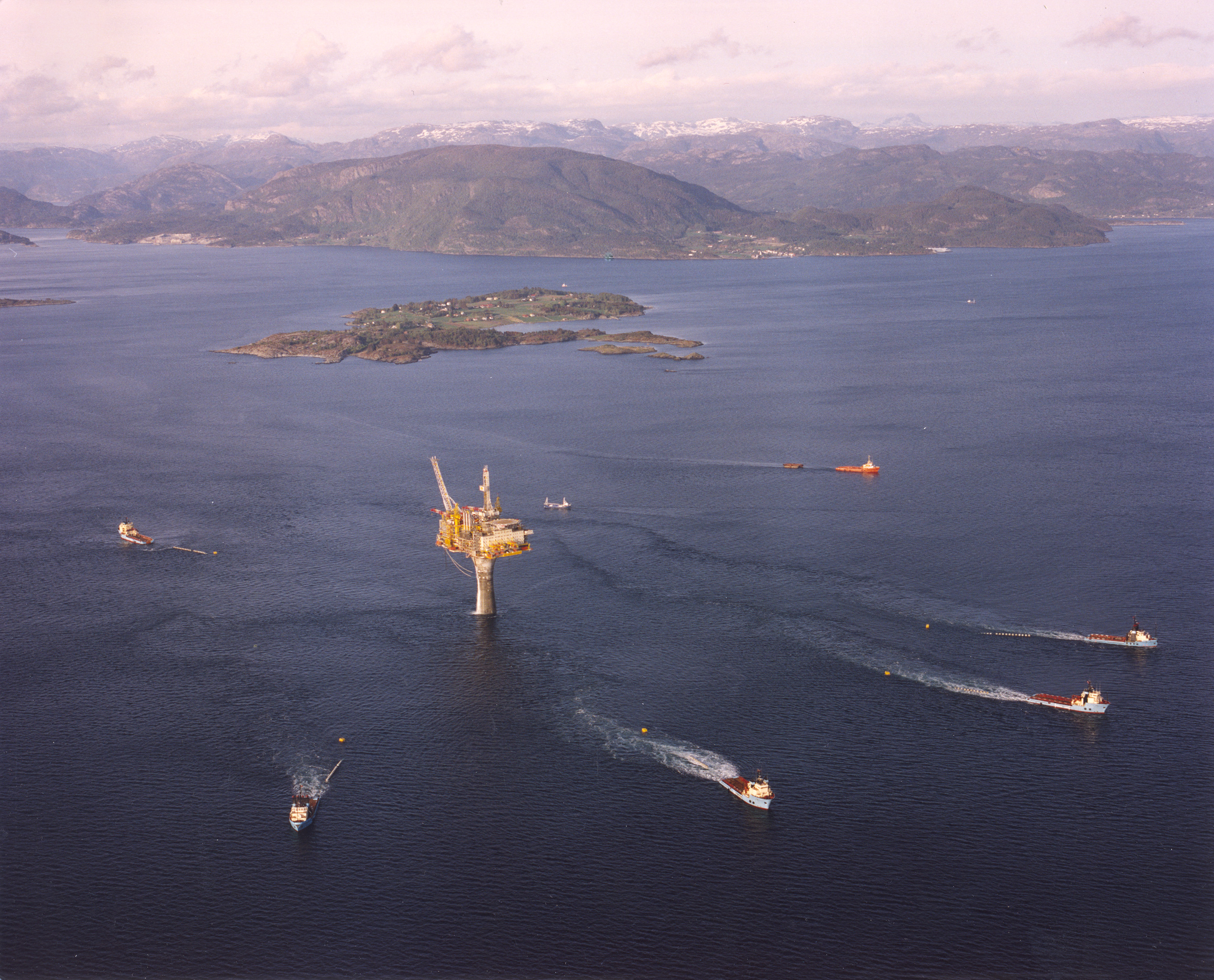
Slepet startet 3. mai i strålende vær. Seks store slepebåter med til sammen 75 000 hestekrefter var nødvendig for å greie de 830 kilometerne til feltet. Dette var den lengste slepedistansen for en Condeep-plattform noensinne og mer enn noen gang var man avhengig av en lang godværsperiode for å gjennomføre et risikofritt slep. Slepet ble gjennomført i løpet av ti dager med en gjennomsnittshastighet på 1,5 knop. Om morgenen 11. mai kl. 04:58 passerte slepet 62. breddegrad med stø kurs for sin endelige destinasjon og 13. mai ankom den sitt faste arbeidssted for de neste 25 – 30 årene. 17. mai 1993 ble plattformen endelig satt på plass og
feiret med et improvisert opptog på helikopterdekket..
Installasjon på feltet
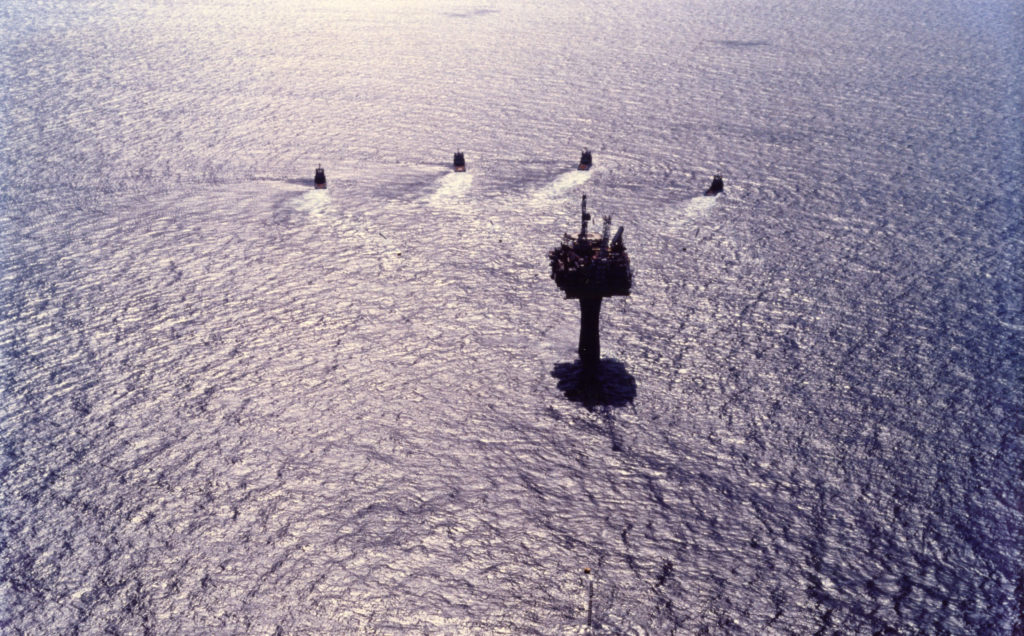
Det var med en viss skepsis man satte i gang slepet tidlig i mai, for på grunn av en feil under støpingen av betongdelen var det oppstått et problem med hensyn til nedsettingen av plattformen på feltet[REMOVE]Fotnote: Intervju med Eivind Wolff (prosjektdirektør for NC) 20.10.2016
Allerede i 1992 var det blitt gjort omfattende sjøbunnsundersøkelser og geoteknisk prøvetakning. Fordi området der plattformen skulle stå viste seg å bestå av veldig bløt leire over lag med fastere leire ble Draugen utstyrt med ni meter lange betongskjørt som skulle sørge for god penetrering.
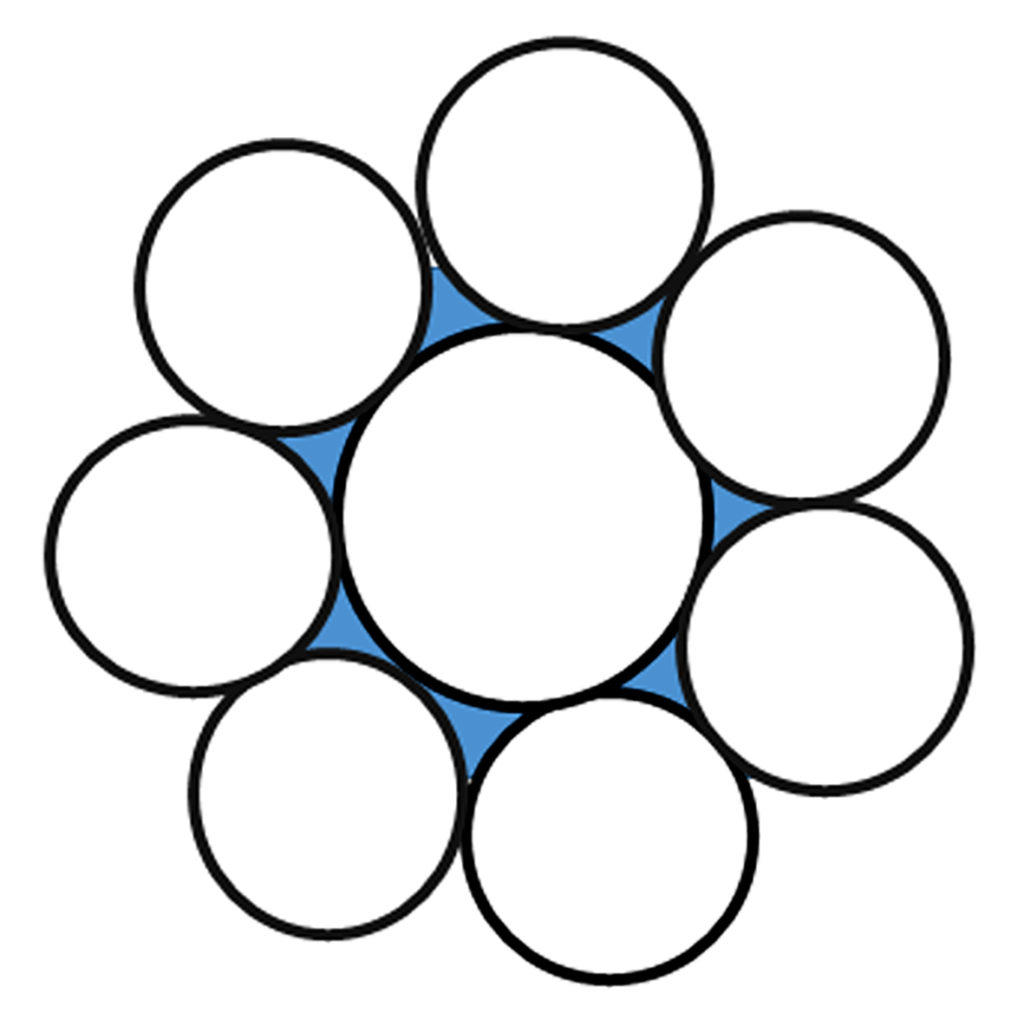
Skjørtene med sine tykke vegger ville fortrenge mye av materialet i sjøbunnen. Dette materialet ville bli presset oppover og fylle alle hulrom under lagercellene, også i de trekantede rommene som dannes når tre sylindriske celler ligger inntil hverandre (se Figur 1). Dessverre ble det under en inspeksjon oppdaget at disse trekantede rommene ikke var hule, men fylt av betong! Da hadde ikke bunnmaterialet noe sted å gjøre av seg når skjørtene trengte ned. Det kunne resultere i grunnbrudd, noe som ville bety at hele plattformfundamentet ville bli skadet og kanskje ubrukelig!
På grunn av støpefeilen og de dårligere enn antatt bunnforholdene ble også området der plattformen skulle stå snevret inn fra en diameter på 20 meter til kun 8 meter.
«Når plattformen ble plassert bare to meter fra ‘bulls eye’ startet ballasteringen for å få skjørtene langt nok ned i havbunnen. Normalt skulle dette være en relativt enkel jobb – bare pumpe ut vann fra lagercellene slik at det utvendige vanntrykket kunne drive plattformen ned i bunnen. Skjørtene var nesten ferdig penetrert da vi fikk beskjed om at kun halvparten av skjørtene var kommet i kontakt med det harde laget. Det bløte leirlaget var tykkere enn antatt og det hardere laget hadde en svak helling. Dette førte til stor og hektisk møtevirksomhet for å kunne finne en løsning på denne uventede oppdagelsen. For å få «bakkekontakt» og et godt feste med de siste delene av skjørtene i det harde leirlaget måtte plattformen stilles ‘litt på skjeve’ »[REMOVE]Fotnote: E-mail med Sigbjørn Egeland (Shells byggeansvarlige for betongdelen) 14.02.2017
Dette ble veldig utfordrende. Metoden som ble valgt var å justere undertrykket inne i cellene slik at det oppstod trykkforskjeller på ulike sider av plattformen. Dette var en omfattende og vanskelig prosess. Ingen hadde gjennomført en slik operasjon i praksis tidligere og det var komplisert å beregne hvor mye trykkforskjell som måtte til. Det måtte gjøres pent og rolig og arbeidet tok minst en uke mer enn en vanlig nedsetting.
Resultatet ble at Draugen ble installert ca. 0,3 grader skjevt («tror det nøyaktige tallet var 0,296 grader»). Det virker kanskje ikke så mye, men på en 300 meter høy plattform blir dette ca. 1,5 meter i horisontalplanet noe som betød at heisene måtte justeres. I tillegg måtte boretårnet justeres for å kunne gjennomføre planlagte boringer.
De som klagde mest var de som spilte biljard – alle kulene la seg i ett hjørne![REMOVE]Fotnote: Intervju med Bjarne Jensen (Shells survey representant for installasjonen av Draugen plattformen) 11.11.2016
Mating av dekket på DraugenProduksjonsstart