Plattformen – et unikt konsept

Valg av løsning
De fire alternativene var:
- En bunnfast plattform av betong med et integrert dekk
- En halvt nedsenkbar (semi-sub) produksjonsplattform med lagringsmuligheter i et eget skip
- En værbestandig skipsformet produksjonsplattform med muligheter lagring og lossing av olje (FPSO)
- To ombygde boreplattformer
Disse fire alternativene skulle så i løpet av ett års tid være gjenstand for ytterligere detaljering og sammenlignes i forhold til gjennomføringsplan, prosjektøkonomi, generell driftsoptimalisering og viktige usikkerhetsmomenter ved den foreslåtte teknologien. Alle fire konseptene skulle dekke de samme driftsforutsetninger med hensyn til produksjonskapasitet, brønner og transportkapasitet.
Shell vurderte ulike typer løsninger, flyter, jacket, GBS, osv, og Norwegian Contractors (NC) (se egen artikkel) gjorde sine hoser grønne i konkurranse med andre konsepter. De hadde jo hatt stor suksess gjennom 1970- og 80-tallet med blant annet Statfjord og Gullfaks.
Dag N. Jensen (construction manager fra NC) forteller:
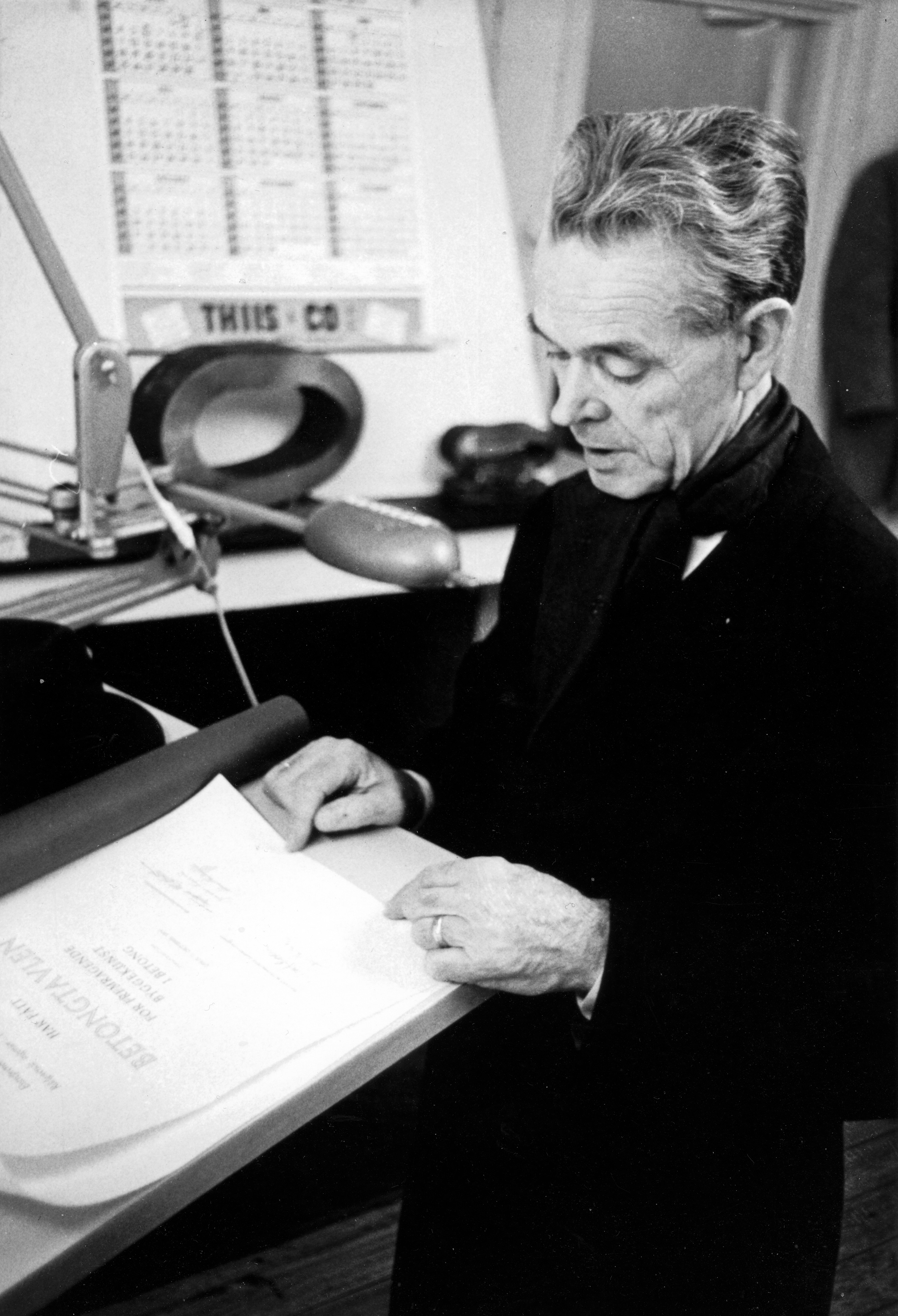
Så ringer Shell til meg, jeg tror det var Serge Leijten, og forteller at nå har de konkludert med at en semi er det beste alternativet. Vi, altså NC, kunne ikke gi oss så lett, så jeg forteller Shell der og da at vi har en bedre løsning og avtaler et møte hos Shell i Stavanger kl 8 neste morgen. Deretter snakker jeg med Tor Ole Olsen i firmaet Dr. Techn. Olav Olsen og vi blir enige om å lage en ett-tårns plattform. Dr Olsen regner og tegner, Tor Ole legger tegningene i min postkasse i løpet av natten, og jeg tar første fly til Stavanger neste morgen og legger fram tegningene med noen muntlige kost og plan estimater for Shell. Dette vakte så stor interesse at de revurderte konseptvalget, ba om ytterligere dokumentasjon og endte opp med å velge en GBS.[REMOVE]Fotnote: E-mail fra Dag N.jensen 26.04.2016
Denne løsningen var altså en forbedret, men ikke endelig versjon, av det konseptet som ble vist i Plan for Utbygging og Drift (PUD). En løsning med FPSO (ikke semi-sub) var i utgangspunktet den billigste løsning, ble det allikevel anbefalt å velge en bunnfast plattform. Fordi den var det konseptet som best tilfredsstilte de uttalte kravene fra Shell med hensyn til driftssikkerhet og lagerkapasitet. I tillegg viste en økonomisk analyse at det var den bunnfaste plattformen som ga den beste internrenten for de store investeringene[REMOVE]Fotnote: Draugen Field Plan for Development and Opreation Appendix VI Concept Selection
Av de ulike design for den bunnfaste betongplattformen – fra ett til fire skaft – var den en-beinte løsningen (monotwer) den billigste løsningen som også ga nok understøttelse til dekks-konstruksjonen og også ga nok rom for de 10 brønnene som skulle føres opp til prosessanlegget.
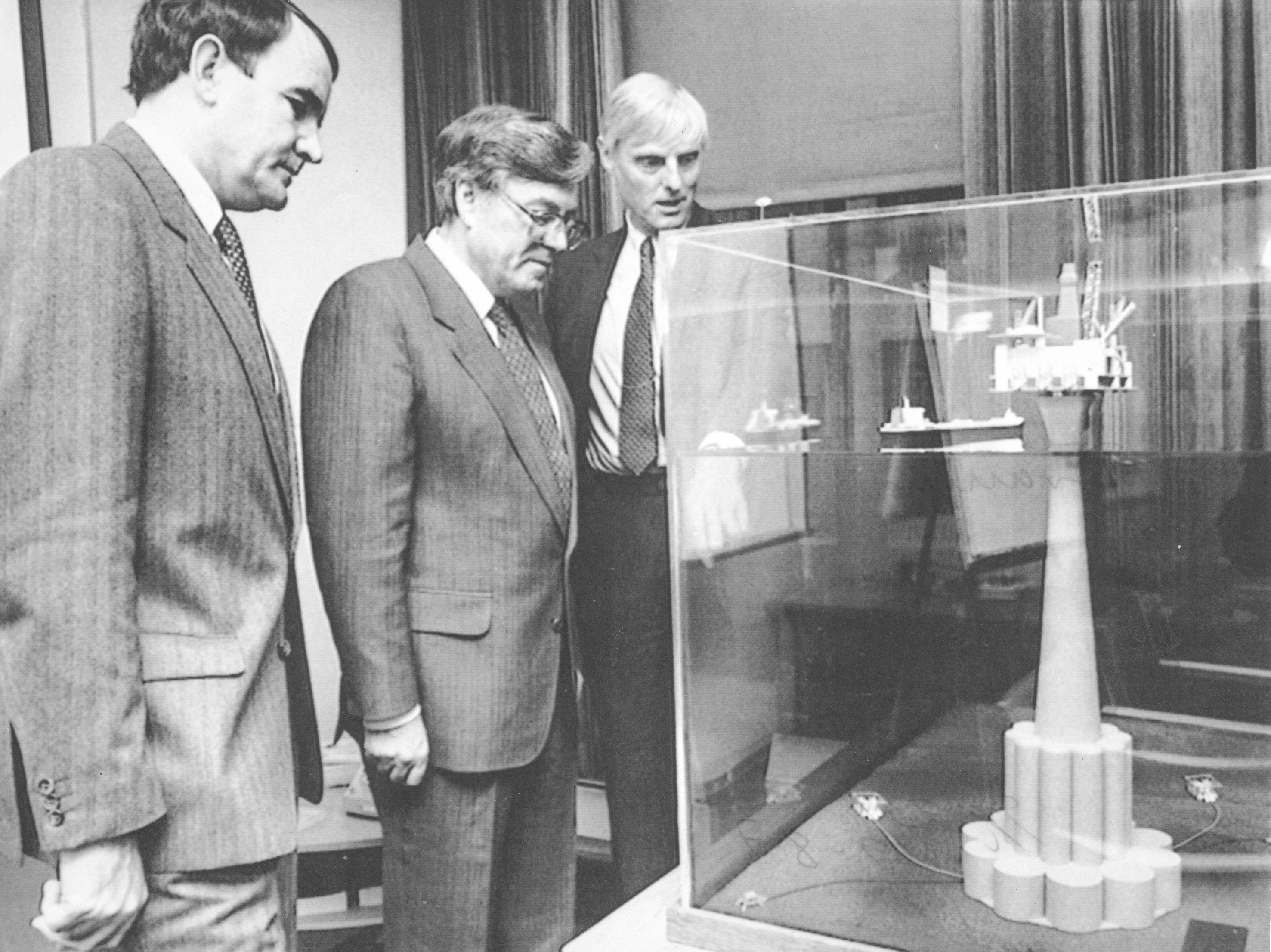
Samtidig ble det viktig å vise at risikonivået for å bore brønner og ta opp og produsere olje samtidig i det ene skaftet var innenfor de sikkerhetsmarginer som krevdes. Det ble gjennomført risikoberegninger som viste at risikoen for ulykker ved en løsning med ett skaft, ikke var vesentlig forskjellig fra ulike løsninger med flere skaft. I tillegg viste disse beregningene at risikonivået for en samtidig boring og produksjon var det samme for de ulike designene.[REMOVE]Fotnote: Draugen GBS Shaft Safty Study (report No. ST-91-CR-018-01 SikteC A/S august 1991
Kravet til betongkonstruksjonen var at den skulle kunne bære en dekksvekt på 22 000 tonn og ha lagerplass til en million fat olje.
Plan for utbygging og drift (PUD) ble sendt i september 1987 og godkjent i Stortinget 19. desember 1988.
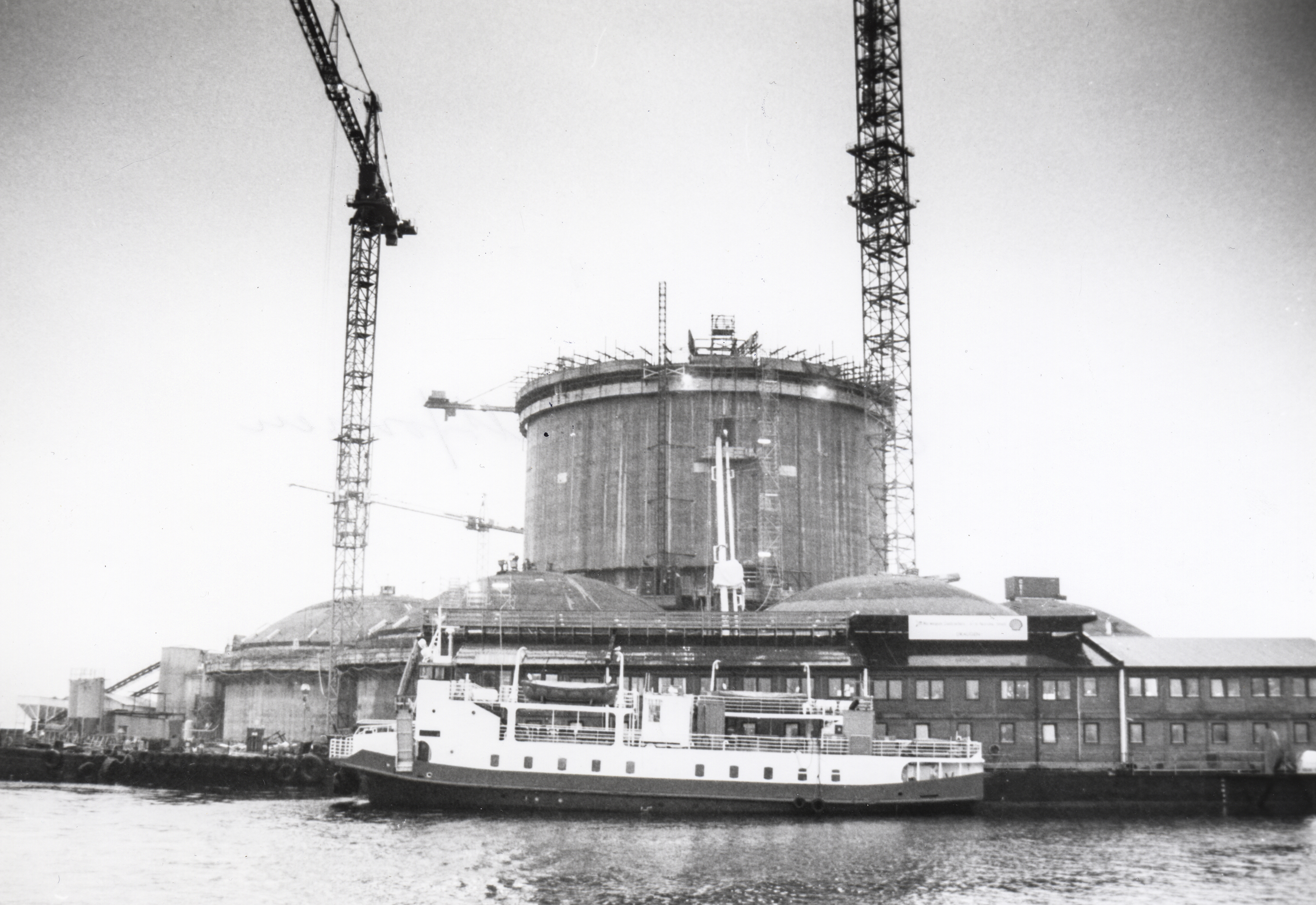
Shell ville prøve å unngå at den tradisjonelle leverandøren av betongplattformer – Norwegian Contractors – skulle være det eneste alternativ. Derfor ble det forsøkt å skape konkurranse gjennom å invitere Peconor, en gruppe bestående av flere selskaper blant annet Skanska, til å komme med anbud på byggingen. Det var den opprinnelige versjonen som ble vist, men Peconor ble oppfordret til å finne fram til et optimalisert design (slik NC allerede hadde lagt fram). Det viste seg at Norwegian Contractors endelige tilbud var langt lavere og dermed kunne NC beholde sitt monopol på bygging av store betongplattformer.
Konseptet med en betongplattform med ett skaft var ikke en helt ny ide. Allerede i 1975 ble det lagt planer på Heimdal-feltet som skulle benytte seg av en slik plattformløsning.[REMOVE]Fotnote: Jøssang, L., & Grønnestad, D. (2016). Heimdal. Bergen: Fagbokforl. Heimdal ble bygd ut tidlig på 1980-tallet med en jacket løsning.[REMOVE]Fotnote: Jacket er en bærende plattform utført som fagverk i stål
Etter PUD-innlevering ble det satt i gang en optimalisering av understellet. Det viste seg at det ville være mulig å bygge sylindre med større diameter. Fram til da mente man at skallkonstruksjonen ikke kunne ha større diameter enn ca. 30 meter. Ved å øke diameteren kunne man flyte på skaftet alene og dermed få lavere tanker som ga nok lagervolum. I tillegg økte man skjørtlengden (den delen som skulle trenge ned i havbunnen) for på denne måten sikre en bedre innfesting for å motstå bølgekreftene (egen artikkel). Det store skaftet utgjør altså flytelegemet for plattformen ved utslep. Dette innebar at man fikk til en løsning som ga betydelig lavere betongvolum og vekt. Et annet gunstig forhold var at vanndypet i utslepstraseen var meget gunstig i forhold til høyden på plattformen. Dette kunne utnyttes fullt ut slik at fribordet ble relativt lavt ved utslep. Dette ga god stabilitet og sikkerhet.[REMOVE]Fotnote: Steen, &. (2002). Den frie tanke : Om kreativ frihet og en ledende norsk ingeniør. Lillestrøm: Byggenæringens forl.: 110-112.
Resultatet ble som vist på Figur 2. I løpet av byggeperioden inntraff det også to viktige hendelser som skulle få innflytelse på utforming og gjennomføring av prosjektet. Både resultatene fra modellforsøk på en annen plattform – Heidrun, og ikke minst havariet av understellet til Sleipner A-plattformen (se egne artikler – Sleipner-havariet og Ringing fenomenet). Kontrakten ble undertegnet september 1989 og byggingen startet i juli 1990.
Normalt hadde man gjort seg ferdig med glidestøpingen i Gandsfjorden i nærheten av NCs anlegg i Hinnavågen. For Draugen (og senere Troll) måtte man endre denne praksisen. På det dypeste er Gandsfjorden (fjordarmen som strekker seg fra Stavanger til Sandnes) mer enn 400 meter dyp. Imidlertid er det ved utløpet av fjorden en «terskel» som er mye grunnere (hvor grunt?) som gjør at plattformene ikke kunne stikke mer enn 70 meter. Derfor måtte man stoppe gliden når skaftet var ca. 50 meter høyt.
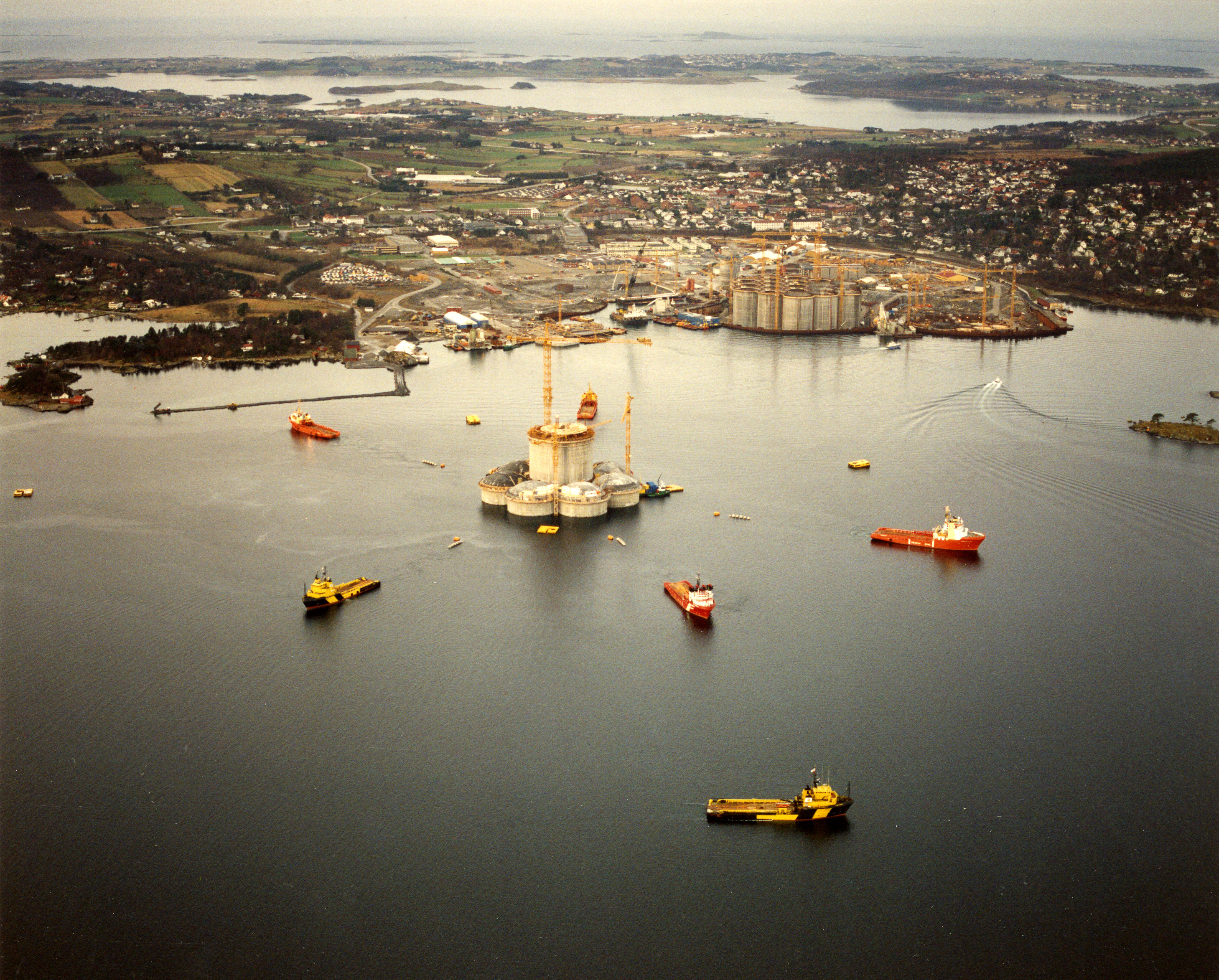
Deretter ble den «halvferdige» plattformen slept til Vats hvor den avsluttende støpe- og utrustningen av skaftet ble foretatt. Vats var også stedet der dekket ble plassert på toppen av skaftet – den såkalte matingen.
Boikott får konsekvenser«Skal denne byen dø?»