Bygging av betongdelen

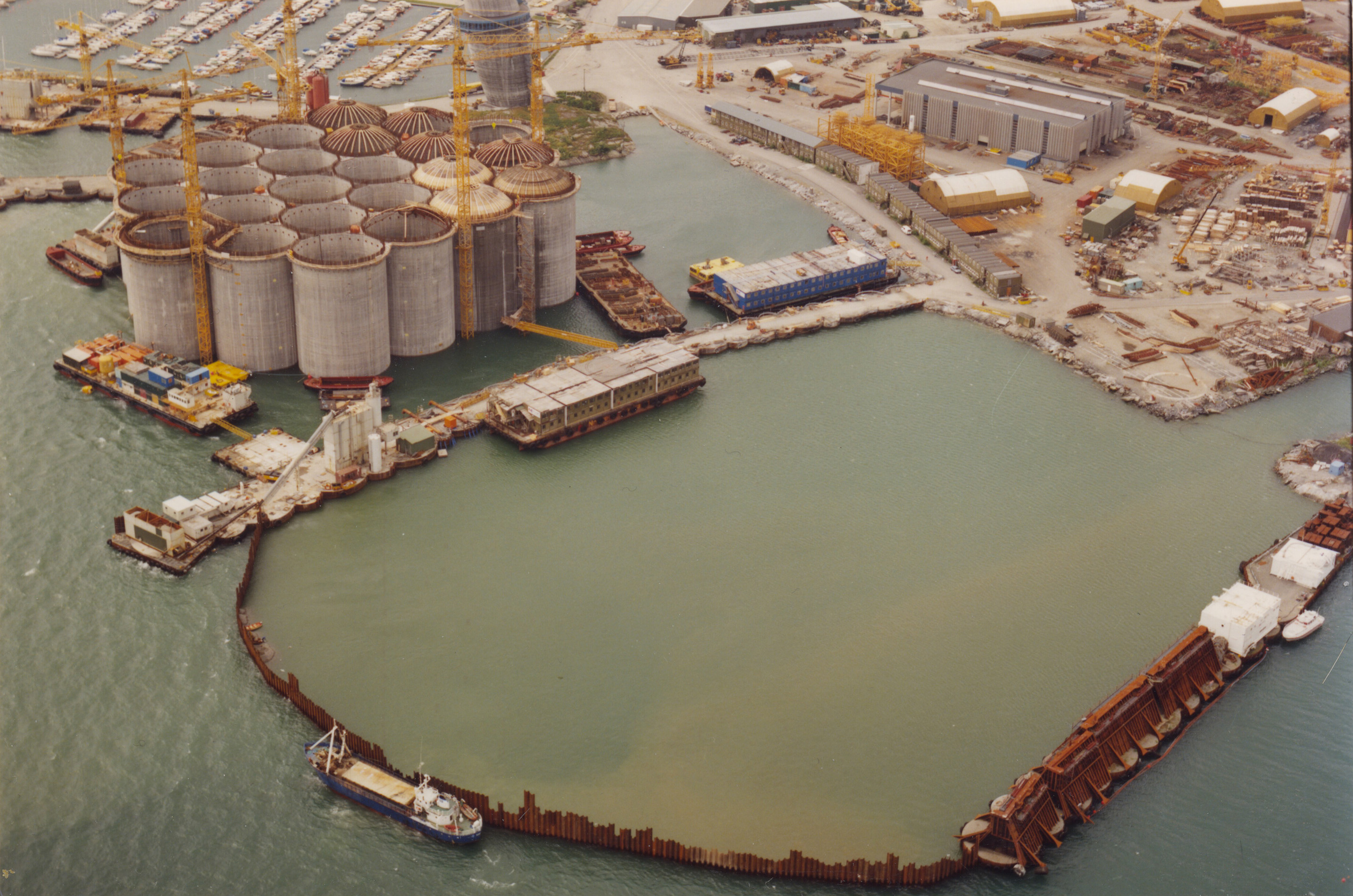
I juni 1990 ble spuntveggen bygd samtidig som man planla utslepet til Gandsfjorden (rett utenfor Jåttåvågen) av Gullfaks C-cellene fra tørrdokken som utgjorde nærmeste nabo. På fjorden lå allerede understellet til Sleipner A. I løpet av sommeren var dokken tørrlagt og arbeidet med de 7 lagercellene og det sentrale bæreskaftet kunne starte i august.
Det første som måtte støpes var skjørtene på 9 meter som skulle sørge for at plattformen kunne forankres og stå trygt i all slags vær ute på feltet. Samtidig ble også støpingen av ankerfestene til Snorre-plattformen bygd på to lektere som var fortøyd ved siden av tørrdokken. Dette var ekstremt travle dager for Norwegian Contractors (NC) siden man bygde fire veldig ulike plattformer samtidig!
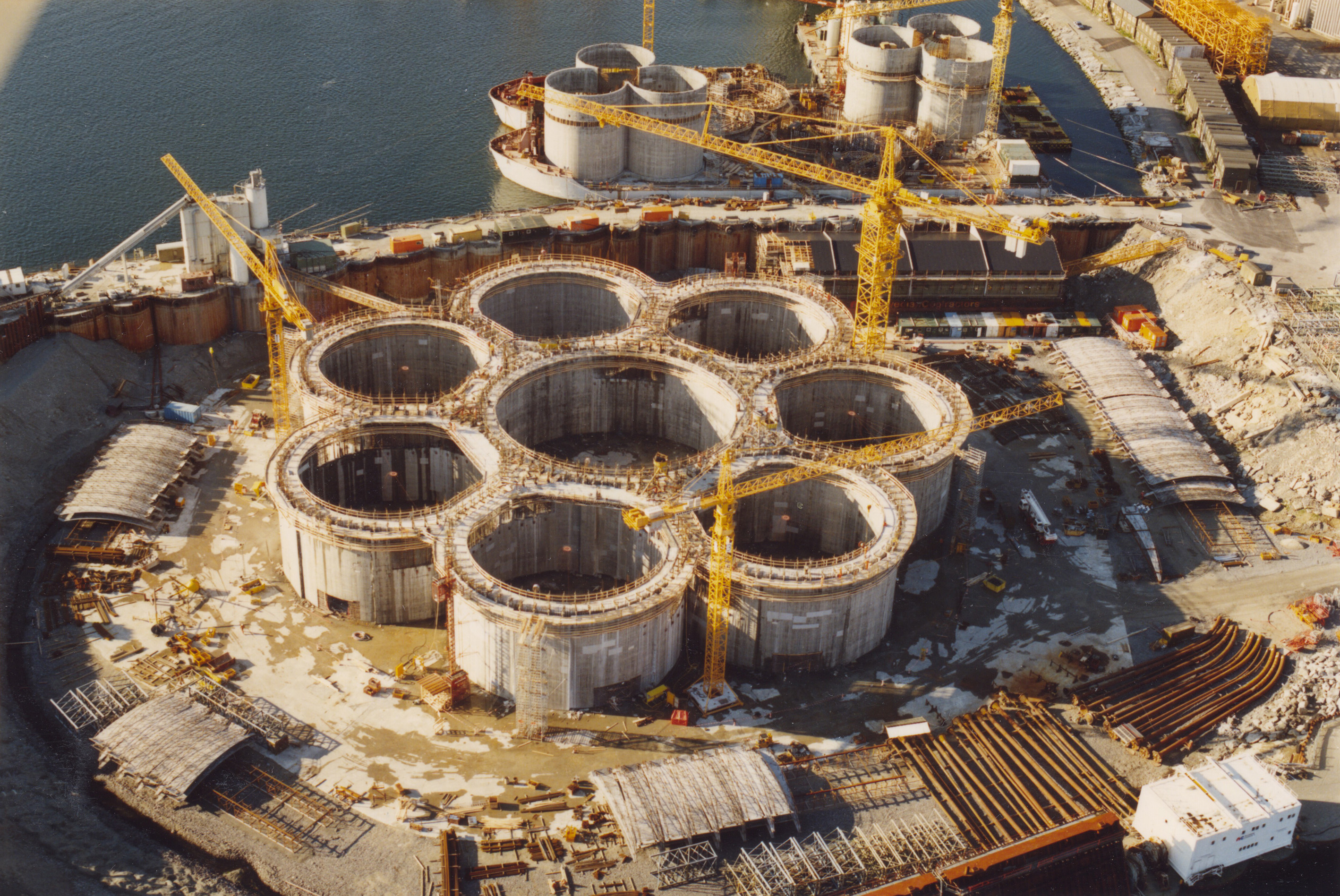
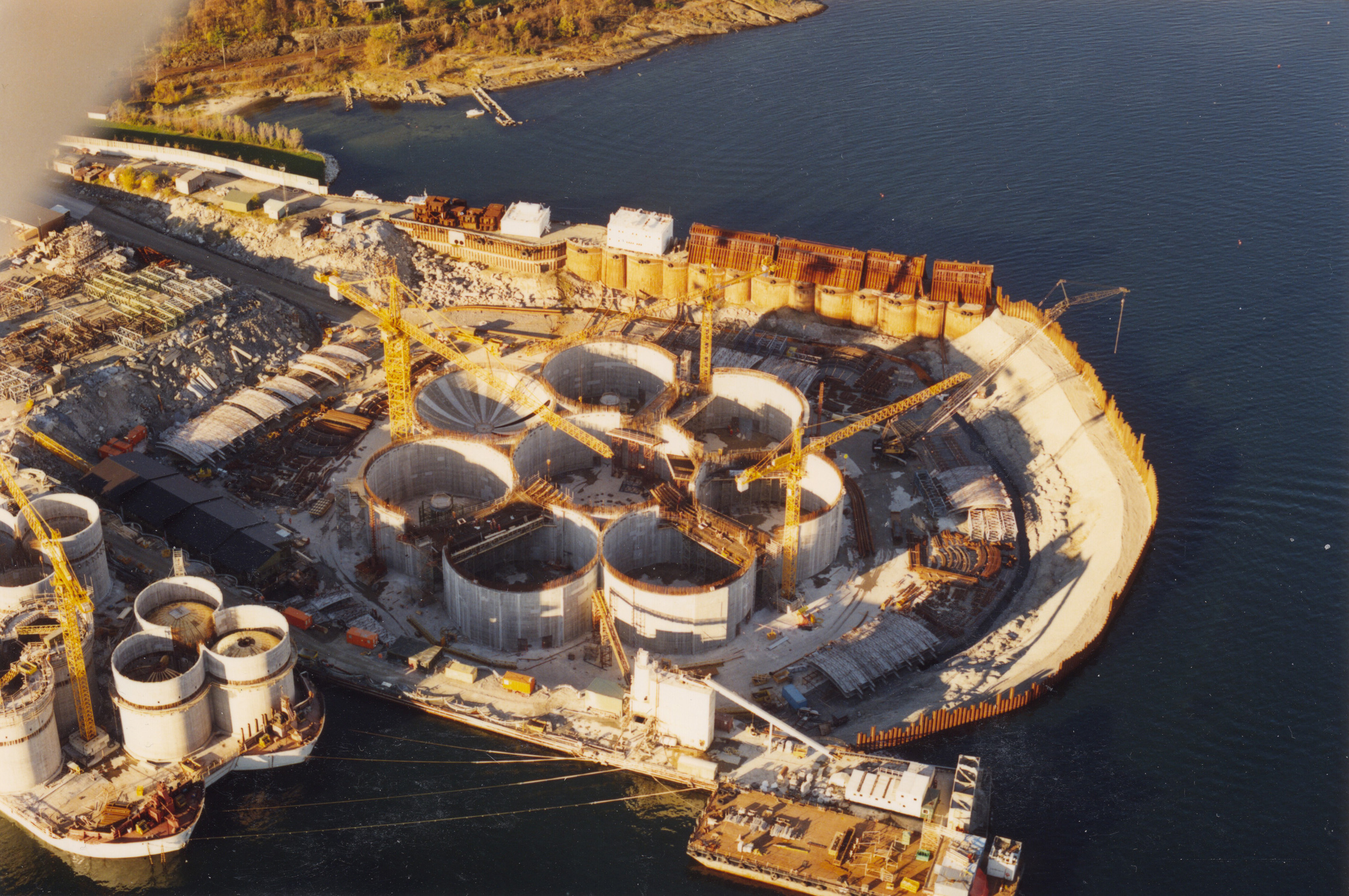
I oktober var skjørtene ferdigstøpt og arbeidet med å gjøre klar forskalingene til selve lagercellene kunne starte. Før støpearbeidet kom skikkelig i gang, ble de første mekaniske installasjonene i bæreskaftet satt på plass i februar 1991.
Nedre del av plattformen består av syv oljelagerceller som ligger rundt den midtre cellen som er nedre del av tårnet. Rør som fører oljen til og fra lagercellene går gjennom celleveggene og inn i midtcellen der de munner ut i et samlerør (manifold) som er 80 cm i diameter. Denne er formet som en smultring med diameter på omtrent 30 meter. Alle rørene er laget av glassfiberarmert plast som er omstøpt med armert betong.
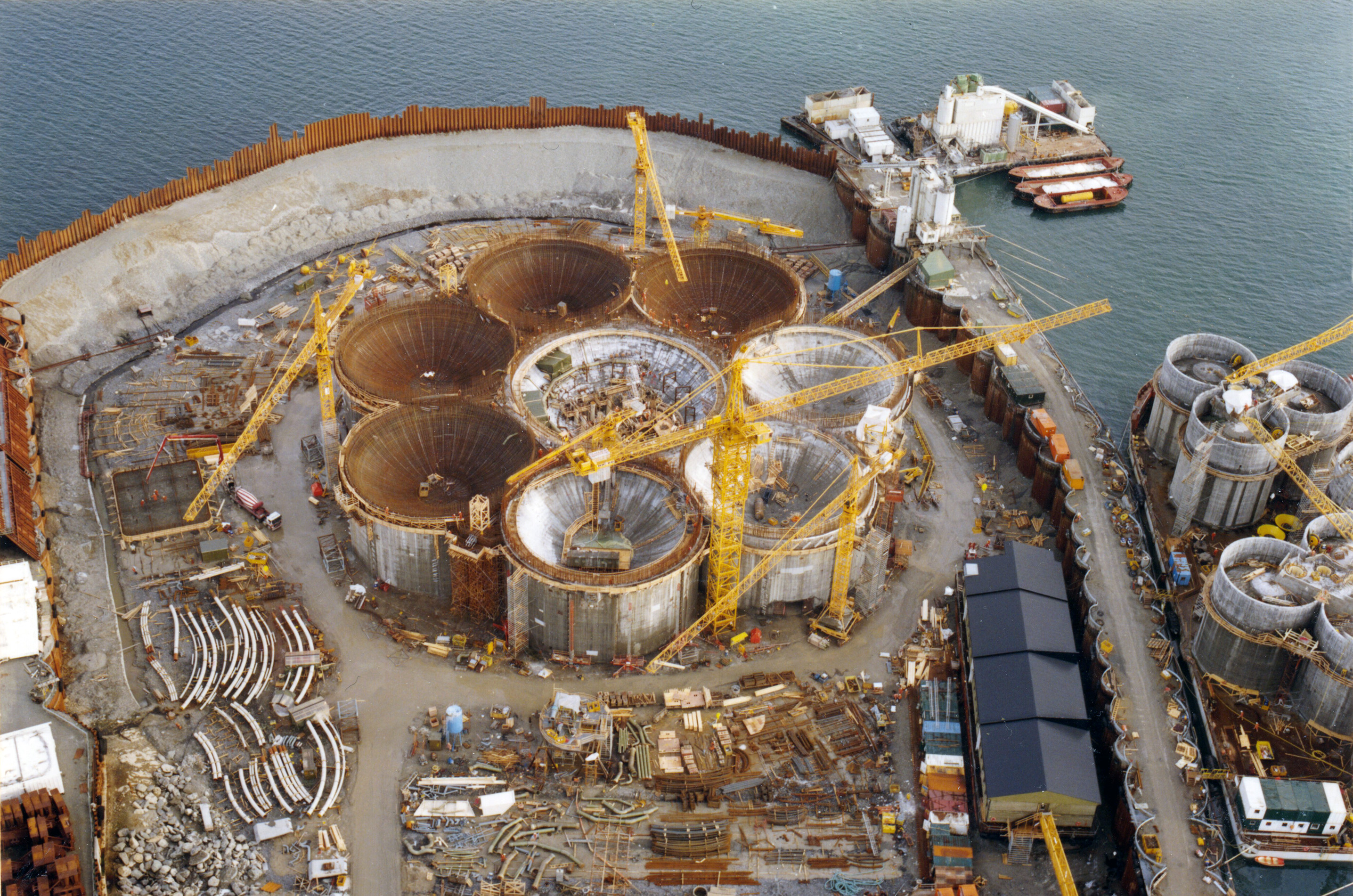
Fra manifolden går et rør med en diameter på 65 cm som fører oljen opp til dekket for behandling/prosessering og videre transport til en lastebøye. Under trykkprøving av dette rørsystemet ble det oppdaget en lekkasje i den innstøpte manifolden, som måtte tettes.
Reparasjonsmetoden som ble valgt var å sende ned folk i det smale røret fra ca. 4 meter over manifolden. Disse gutta hadde med seg alt de trengte for å reparere lekkasjen med epoxy.[REMOVE]Fotnote: Epoxy, eller kunstharpiks, er en flytende plastmasse som danner forbindelser til underlaget slik at massen blir sittende fast og fungerer som lim. Bare det å få plass til en mann på taustige ned et så trangt rør, ble ansett som nærmest umulig, men disse fyrene greide det! Og at de greide å ta seg frem til lekkasjepunktet med verktøy og tilbehør i et 80 centimeters rør var jo også en bragd. Men de klarte det, og kom seg helskinnet ut. De hadde med seg videokamera for å kunne dokumentere reparasjonen, og på et av opptakene, der de sitter krumbøyde på verdens trangeste arbeidsplass, kan vi se og høre en av dem si med et flir: «This is a pipe show!»
En av de teknologiske nyvinningene på Draugen var at de aller fleste rørsystemene var av glassfiberarmert plast. Dette var en bra utvikling, men det innebar noen overraskelser for NC som ikke var vant med dette materialet, innrømmer NC prosjektdirektør Eivind Wolff.
– Mens stålrør nærmest kan garanteres å være tette, innebar skjøtene i plastrørene en risiko for lekkasje, som vi ikke kunne se bort fra. Og med et betydelig trykk i de innstøpte rørene, kunne vi risikere at betongen simpelthen ville revne. En betydelig økning av armeringsmengdene måtte til for å dokumentere at veggene var sterke nok.[REMOVE]Fotnote: Intervju med Eivind Wolff (prosjektdirektør for NC) 20.10.2016
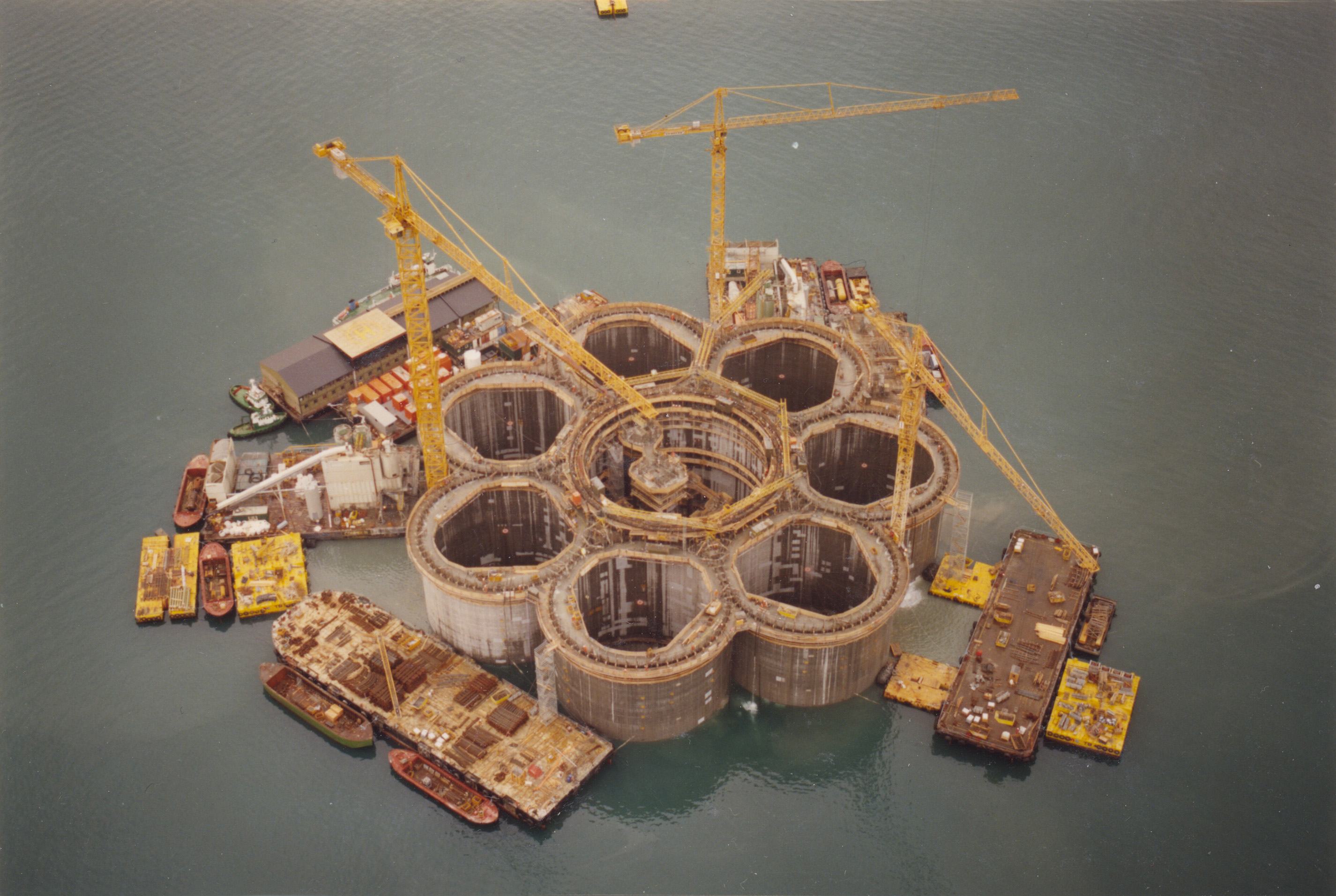
Så fulgte tre hektiske måneder hvor skaftene ble støpt opp til ønsket høyde før utfløting av dokk. Spunteveggen i tørrdokken ble fjernet og luft ble pumpet inn i rommet som ble dannet under skjørtene for å gi konstruksjonen nok oppdrift til å fløtes ut på fjorden.
Etter at plattformen var blitt trygt forankret i Gandsfjorden i løpet av juni, begynte man å støpe bæreskaftet opp til planlagt høyde – 70 meter over framtidig havbunnsnivå (altså ikke medregnet skjørtene). Samtidig gjorde man også klar lagercellene slik at domene (som utgjør taket på cellene) kunne forskales.
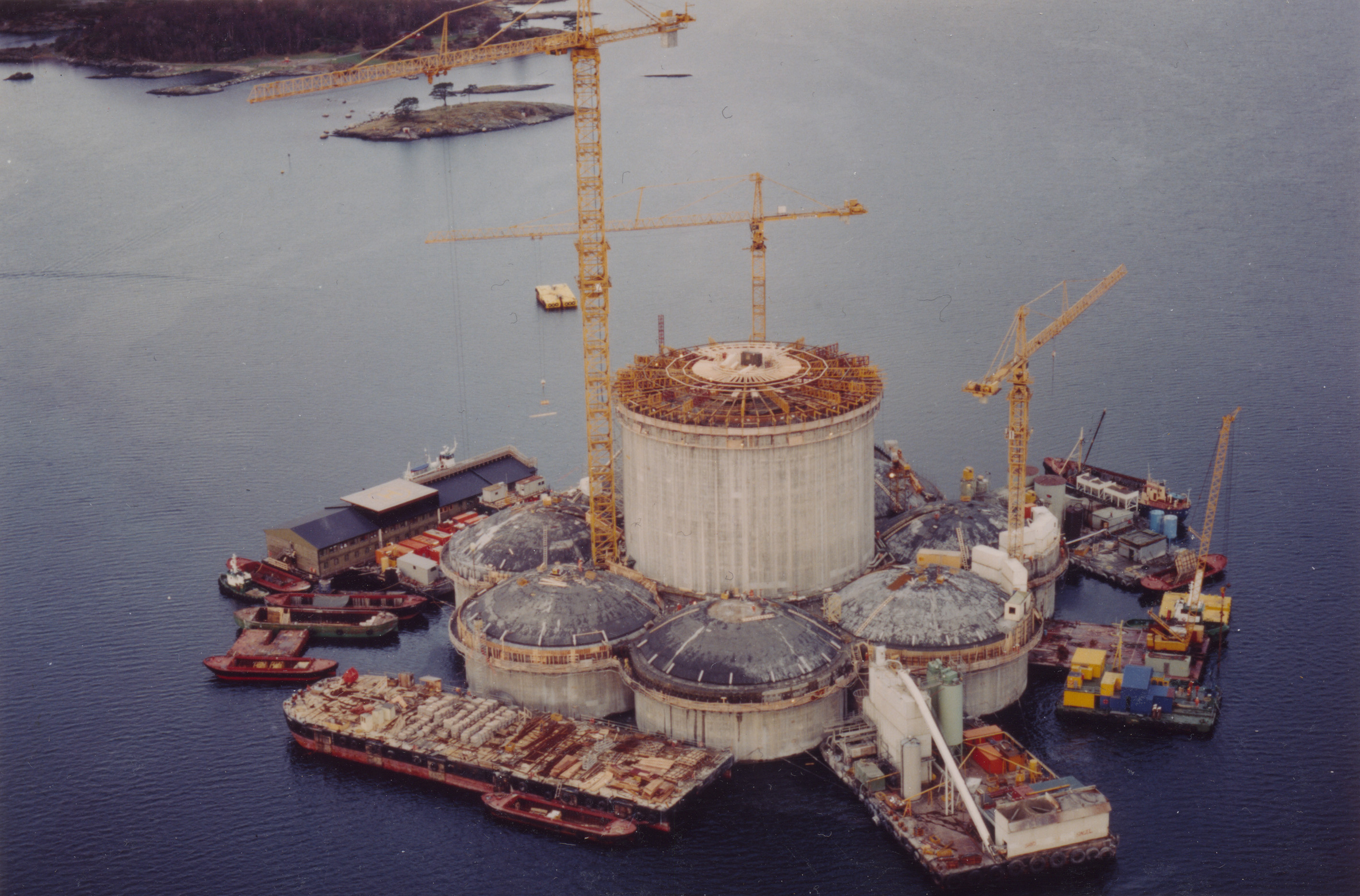
Fra august og ut resten av 1991 ble lagercellene gjort ferdig og ytterligere utrusting av bæreskaftet ble installert. Men ytterligere overraskelser skulle ramme Draugen-prosjektet.
Om morgenen 23. august forsvant Sleipner plattformen i dypet og alle som var involvert i de ulike prosjektene som var i gang ble veldig bekymret for hva som hadde skjedd og om det ville få noen virkning på blant annet Draugen. I et intervju med Stavanger Aftenblad ga imidlertid Shells prosjektdirektør Mahdi Hasan uttrykk for at hans selskap hadde full tillit til NC og at de ikke så noen grunn til bekymring for framdriften i prosjektet.[REMOVE]Fotnote: Stavanger Aftenblad. (1991. 4. september). Shell har tillit til NC.
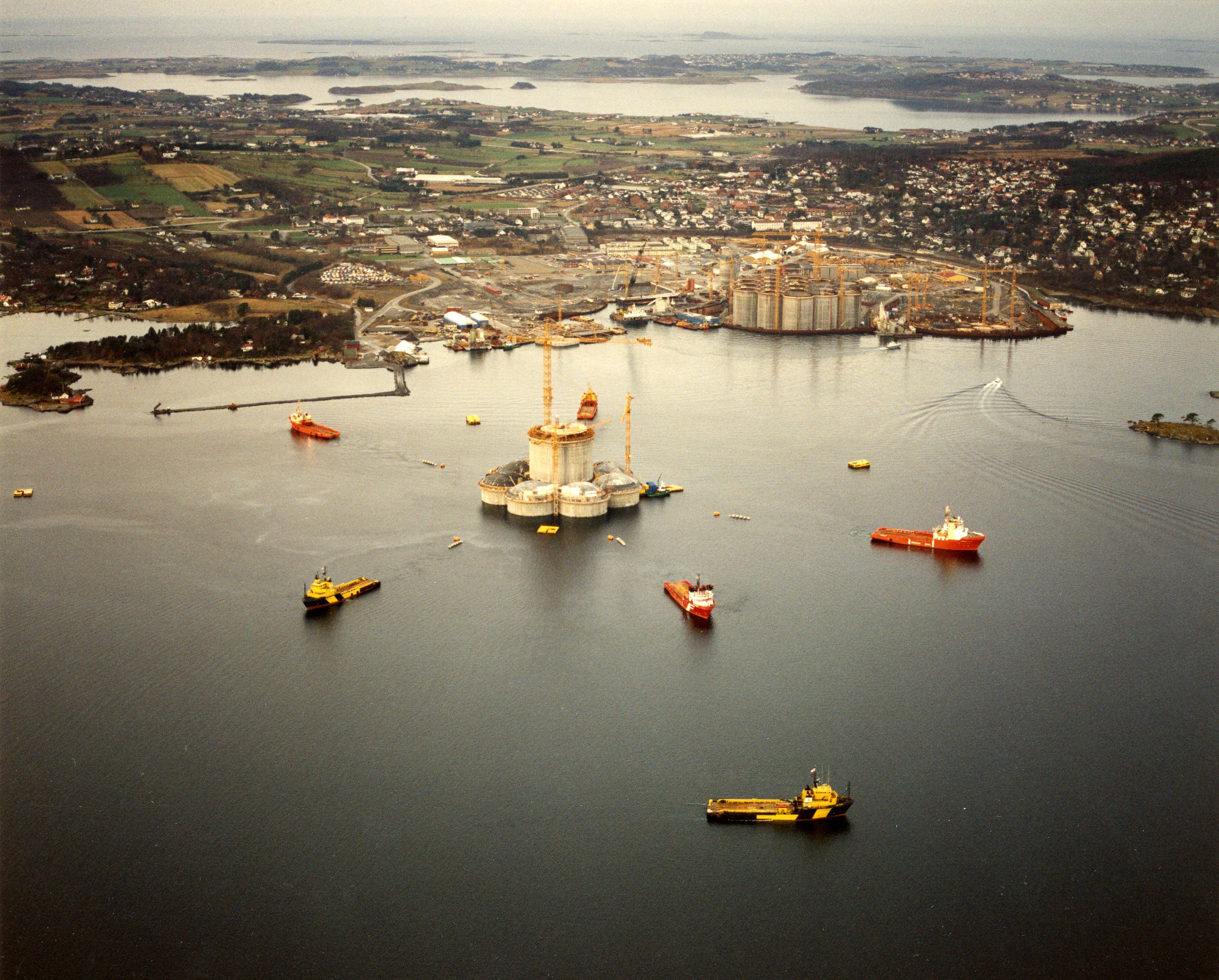
I løpet av januar 1992 ble konstruksjonen gjort klar for sleping til Vats i Yrkesfjorden, der ferdigstillingen av betongplattformen skulle gjøres og sammenkopling (mating) med dekket skulle finne sted. Fordi Gandsfjorden har en vesentlig begrensning ved utslep på grunn av en såkalt terskel[REMOVE]Fotnote: Terskel er betegnelsen på et grunnere område ved utløpet av de fleste norske fjorder. ved utløpet, var det bare de første condeepene Beryl A og Brent B, som ble installert i engelsk sektor, fikk dekkene koblet på i Gandsfjorden. På grunn av Draugens spesielle form og høyde krevde det et større dypgående ved slep slik at terskelen i Gandsfjorden ble for grunn for denne plattformen.
Eivind Wolff forteller: «Det mest spektakulære problemet vi måtte løse, ble oppdaget under forsøk som ble utført på en modell av plattformen på marinteknisk laboratorium i København sommeren 1992. Forsøkene ble utført for å bekrefte at de beregningene som allerede var gjort var riktige. Det 230 meter høye tårnet har form for en kjegle, som øverst vider seg ut til en firkant med flate sider. Modellforsøkene viste at når en høy bølge traff denne flate siden, fikk tårnet et ekstra smell som ga ekstreme krefter nedover i konstruksjonen, med inntil 70% overskridelse av det som var beregnet, og tildels allerede bygget!! Denne voldsomme responsen ble i fagmiljøet omtalt som «nærmest en ny naturkraft». Fenomenet fikk betegnelsen «Ringing», fordi det har likhet med det som skjer når hammeren i et gammeldags ringeapparat treffer selve ringeklokken (les mer i egen artikkel).
Byggingen av tårnet, som allerede var kommet halvveis, ble øyeblikkelig stanset, for å finne mulige løsninger. Dette var en svært dramatisk situasjon, som ingen hadde vært oppe i før, og mange begynte å tvile på om plattformen overhode kunne brukes! Ganske snart ble løsningen likevel funnet. Den besto i å forlenge tårnet så mye at de høyeste bølgene ikke ville treffe den flate betongsiden. I tillegg måtte man øke styrken i selve skaftet. Dette ble ordnet ved at man tok i bruk de ekstra forspenningskanalene som var lagt som reserver i tårnveggen, for det tilfelle at noen av dem skulle bli fylt med betong under støpearbeidene. Vi hadde akkurat nok av disse til å kunne dokumentere tilfredsstillende styrke. Da var det mange som pustet lettet ut!!»
De glassfiberarmerte rørene som er nevnt tidligere, ble også utsatt for en ekstra belastning som ikke var påtenkt under utviklingen av plattformen. Selv om veggen som rørene fra lagercellene går gjennom er over 2 meter tykk, med tungt armert betong, ville disse veggene bli trykket sammen under maksimalt vanntrykk, så mye at plastrørene ikke ville tåle det. Da dette ble oppdaget, var konstruksjonen ferdig støpt, med en total høyde på 289 meter. Og den raget nesten 220 meter over overflaten i Yrkjefjorden. For å hindre at rørene skulle få store skader som følge av stor deformasjon, ble denne nedre delen av plattformen forsterket med mer enn 1000 tonn armert betong. Denne betongen ble laget i et flytende betongblandeverk og heist med kran 220 meter opp til toppen av tårnet, og så ned de ca 280 meterne til innvendig bunn av plattformen.
Eivind Wolf forteller videre: «Plattformen lå fortøyd i fjordkrysset der Vatsfjorden møter Yrkjefjorden, godt synlig fra anleggsområdet på vestsiden av Vatsfjorden. Like etter at bunnforsterkningen var fullført, fikk jeg en telefon fra Norske Shells prosjektleder, som var min motpart under kontrakten. Han utbrøt: «Hva har skjedd med plattformen min, jeg kan ikke se den lenger!!» Jeg kikket ut av kontorvinduet, og trodde ikke mine egne øyne, plattformen var ikke der! Men over det østre neset mot Yrkjefjorden kunne jeg se toppen av tårnet. Det sakk i meg: «Kjettingbrudd!!» Og det var akkurat det det var. En av våre kjempekjettinger hadde røket! Hvert ledd i disse fortøyningskjettingene var over en meter langt, 60 cm bredt og hadde en godstykkelse på over 20 centimeter. Og likevel, brudd. Vi regnet ut etterpå at hadde dette skjedd mens vi skulle sette på dekket, og plattformen hadde et dypgående på over 250 meter, da ville den gått på grunn med skader som det ville vært umulig å reparere, et nytt Condeep-havari!»
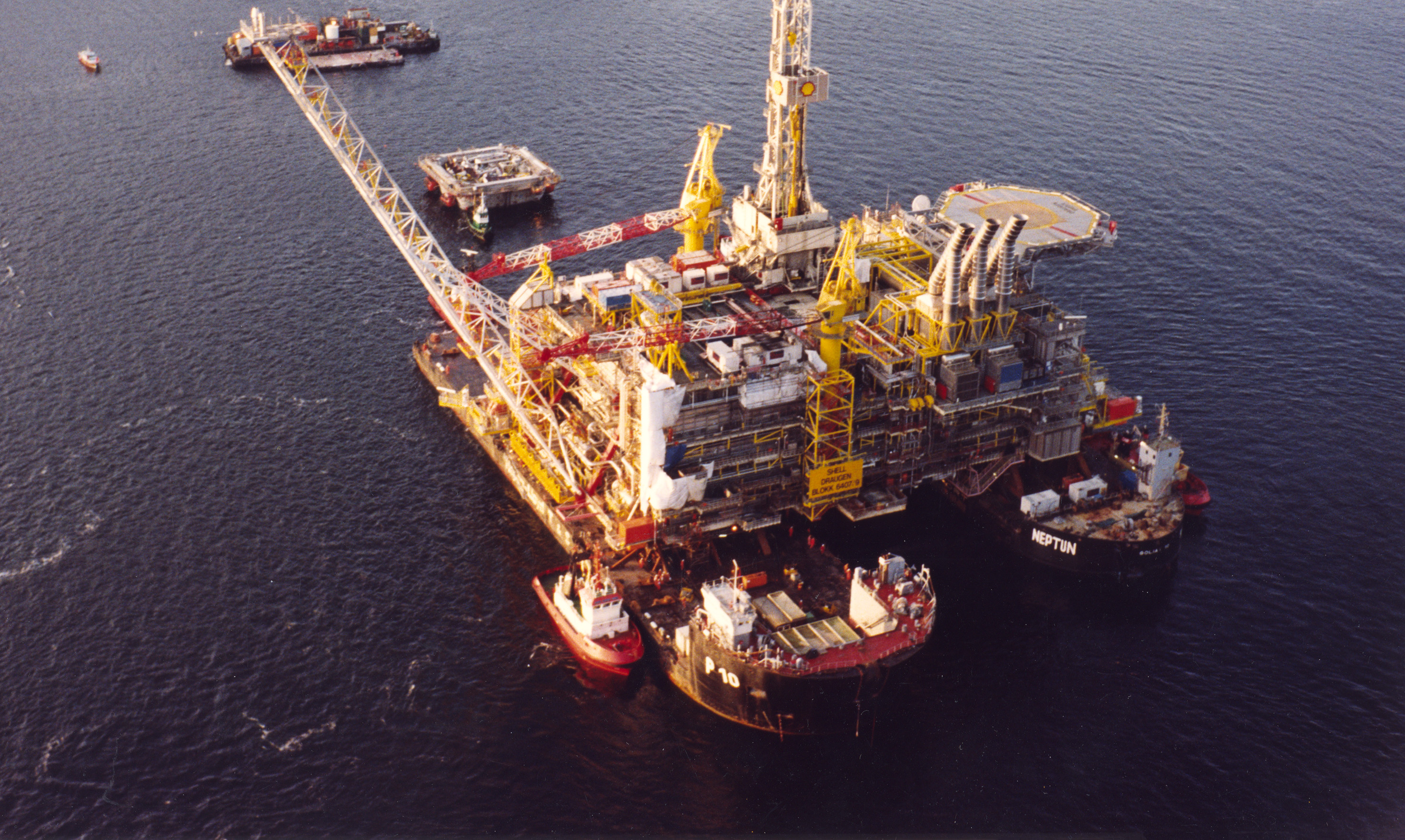
I påvente av resultatene fra modellforsøkene i København og de endringene som ble gjennomført ble sammenkoplingen med dekket utsatt fra den opprinnelige datoen i desember 1992 til 26. mars året etter. Dette førte imidlertid ikke til noen forsinkelser knyttet til ferdigstilling av prosjektet. Det ble bare mindre tid til å kontrollere at alt var som det skulle være med hensyn til oppkopling av rør og kontrollsystemer. Alt så ut til være i skjønneste orden, men som Eivind Wolff forteller:
«Dagen etter den vellykkede sammenkoplingen kommer en av mine nærmeste medarbeidere inn på mitt kontor med et særlig alvorlig uttrykk i ansiktet, og sier: «Du, jeg tror ikke vi greier å installere plattformen på feltet!» Da syntes jeg det fikk være nok av motgang på ett og samme prosjekt, men vi hadde jo løst alle de andre problemene …! Han forklarte at det hadde skjedd en katastrofal feil da underste del av plattformen ble bygget i tørrdokken på Hinna. Skjørtene i konstruksjonen fortsetter 8-9 meter ned under bunnen for å trenge ned i sjøbunnen og bidra til å stabilisere plattformen og overføre krefter. Dette er tykke vegger som fortrenger mye av materialet i sjøbunnen. Dette materialet presses oppover og fyller de hulrom som finnes, bla i de trekantede rommene som dannes når 3 sylindriske celler ligger inntil hverandre. Noen hadde nettopp sjekket hvordan betongen faktisk var støpt i dette området, og oppdaget at disse trekantede rommene ikke var hule, men fylt av betong! Da hadde ikke bunnmaterialet noe sted å gjøre av seg når skjørtene trengte ned. Det kunne resultere i grunnbrudd, noe som ville bety at hele plattformfundamentet ville bli skadet og kanskje ubrukelig!
Nå hadde vi bare noen få uker til å finne en løsning som ville overbevise alle parter. Kartet over sjøbunnen med meget nøyaktig angivelse av dybder i mange punkter der plattformen skulle stå, ble gransket grundig med henblikk på å finne noen litt dypere steder der det ville bli minst mulig masse som skulle fortrenges. Det ble også laget et program for å variere trykket under plattformbunnen slik at jordmassene ble dradd mot områdene under hovedcellene, der det var god plass til dem, og bort fra de trekantede cellene, der det ikke var plass».
Hvordan det gikk med slepet som startet 3. mai og nedsettingen som ble foretatt 16. mai kan du lese om i en egen artikkel.
Foto fra bygging av betongdelen til Draugen
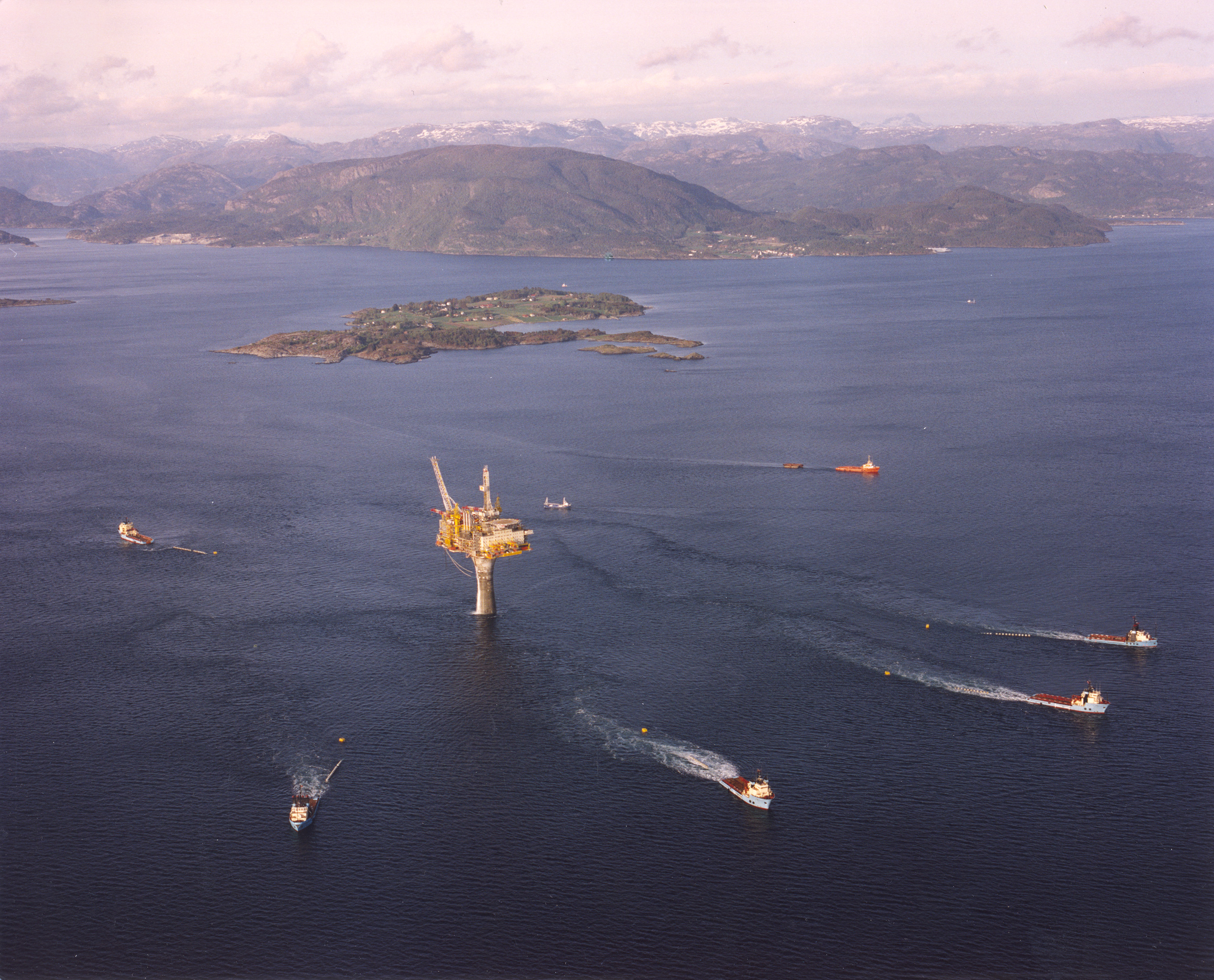