The unique Draugen platform

Four options remained for further consideration in May 1986. These were:
– a fixed concrete platform with integrated topsides
– a semi-submersible platform with attached storage ship
– a weather-adapted monohull production floater with possible oil storage and offloading (FPSO)
– two converted drilling rigs.
This quartet was then subjected to a year of further detailing and comparison with the implementation plan, the economics of the project, general operations optimisation and key uncertainties with the proposed technology. All the options had to satisfy the same operational assumptions in terms of production capacity, wells and transport capability.
While Shell considered various solutions – floater, steel jacket (support structure), gravity base structure (GBS) and so forth – Norwegian Contractors (NC) promoted its concrete option.
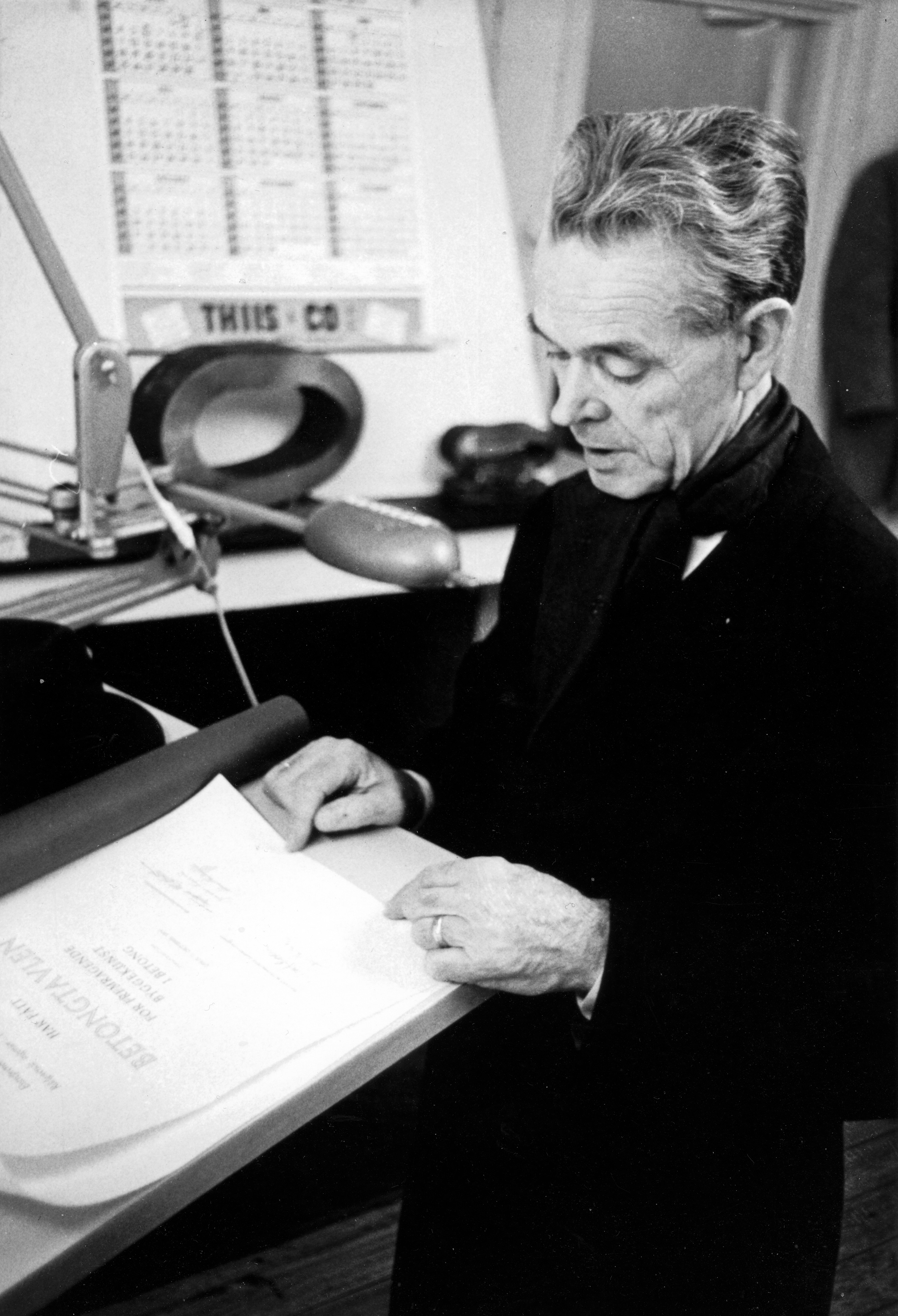
After all, this construction company could point to great success during the 1970s and 1980s with its Condeep design, not least on the Statfjord and Gullfaks fields. NC construction manager Dag N Jensen recalls the process:
Then Shell called me – I think it was Serge Leijten – to say that they had now decided that a semi was the best option. We, in other words NC, could not give up that easily, so I told Shell there and then that we had a better solution and agreed to meet the company in Stavanger at 08.00 the following day. I talked with Tor Ole Olsen at the Dr Techn Olav Olsen consultancy, and we agreed to create a monotower platform. Olav Olsen calculated and calculated, Tor Ole put the drawings in my letterbox during the night and I took the first flight to Stavanger the next day to present the drawings to Shell with some verbal cost and planning estimates. This aroused such great interest that the company revised its choice of concept, asked for further documentation, and ended up going for a GBS.[REMOVE]Fotnote: E-mail fra Dag N.jensen 26.04.2016
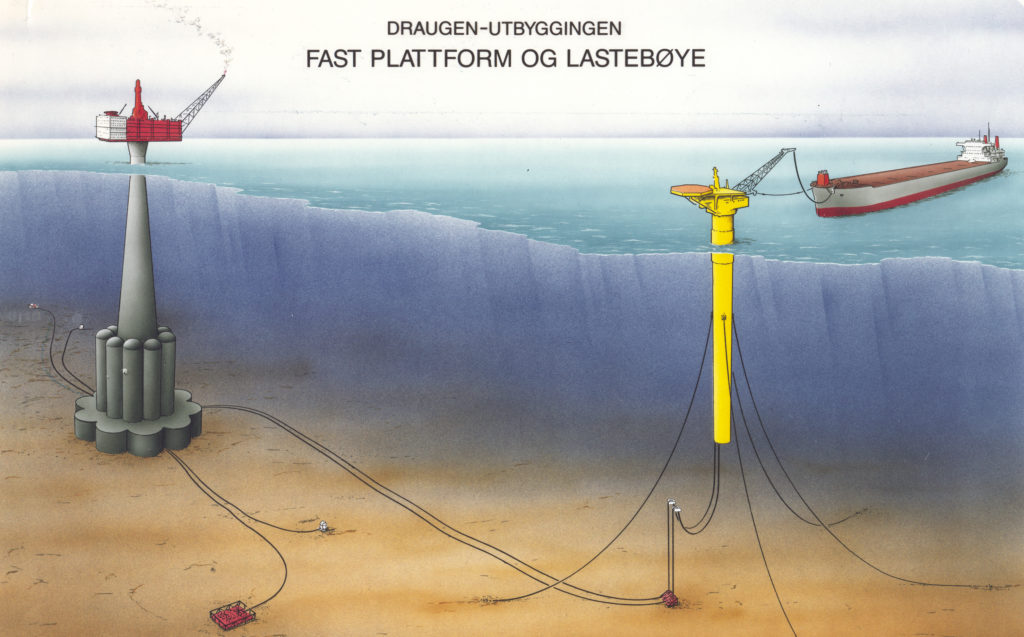
In other words, this solution represented an improved but not final version of the concept presented in the plan for development and operation (PDO) of Draugen. While a monohull FPSO basically represented the cheapest option, a fixed structure was recommended because it best satisfied Shell’s stated reliability and storage requirements. An economic analysis also showed that a fixed installation yielded the best internal rate of return on the huge investment involved.[REMOVE]Fotnote: Draugen Field Plan for Development and Opreation Appendix VI Concept Selection
The cheapest of the fixed concrete GBS solutions, ranging from one to four support shafts, was the monotower. This also provided sufficient support for the topside design and room for 10 wells to be conducted to the process facilities.
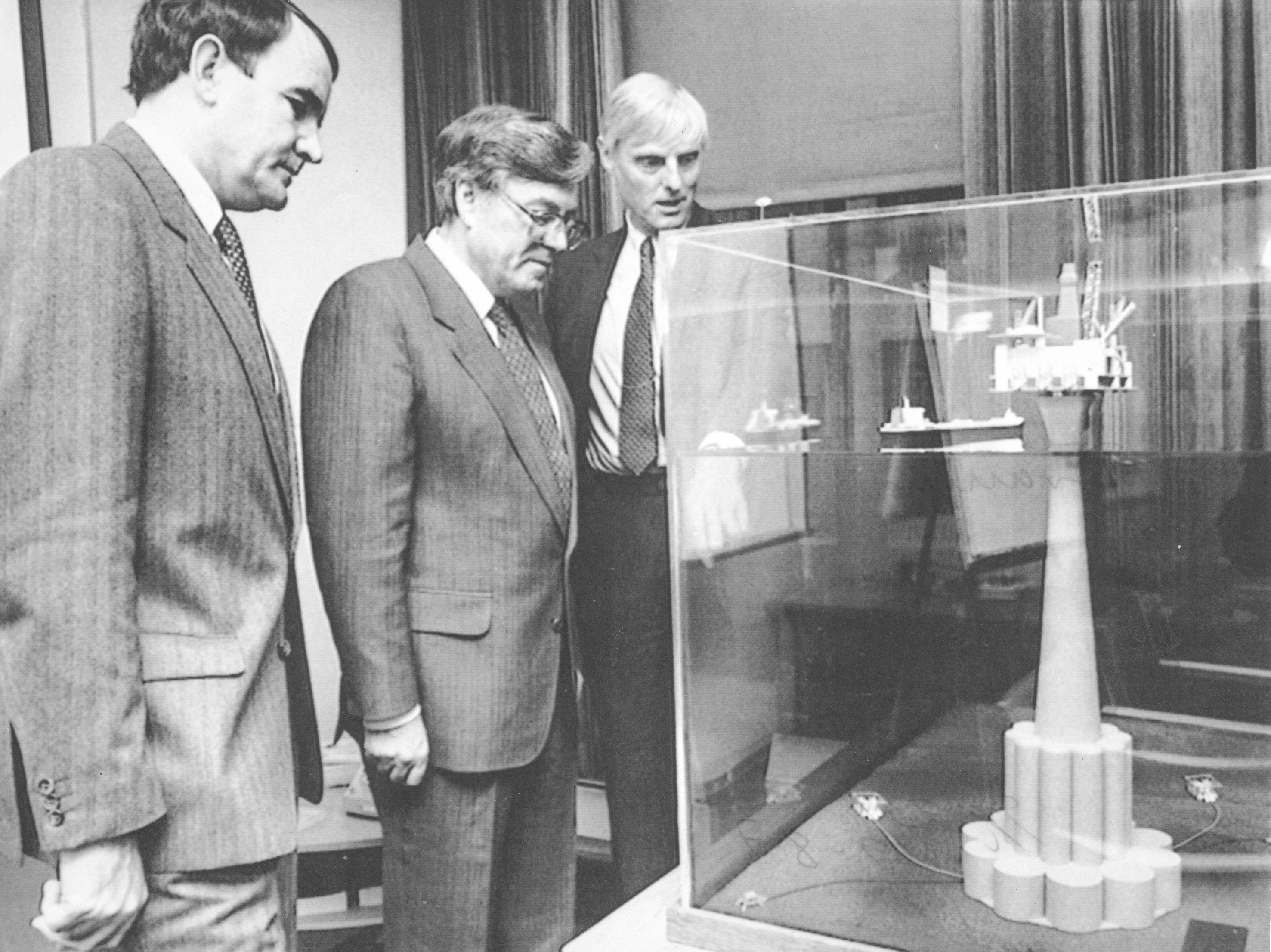
At the same time, it became important to demonstrate that drilling wells and producing oil simultaneously through a single shaft fell within the required safety margins.
Calculations indicated that the risk of accidents with a monotower solution did not differ significantly from alternative solutions with several shafts.
In addition, these assessments showed that the level of risk for simultaneous drilling and production was the same for the various designs.[REMOVE]Fotnote: Draugen GBS Shaft Safty Study (report No. ST-91-CR-018-01 SikteC A/S august 1991
The concrete structure was required to support a topside weight of 22 000 tonnes and to store a million barrels of crude oil.
Submitted in September 1987, the PDO for Draugen was approved by the Storting (parliament) on 19 December the following year.
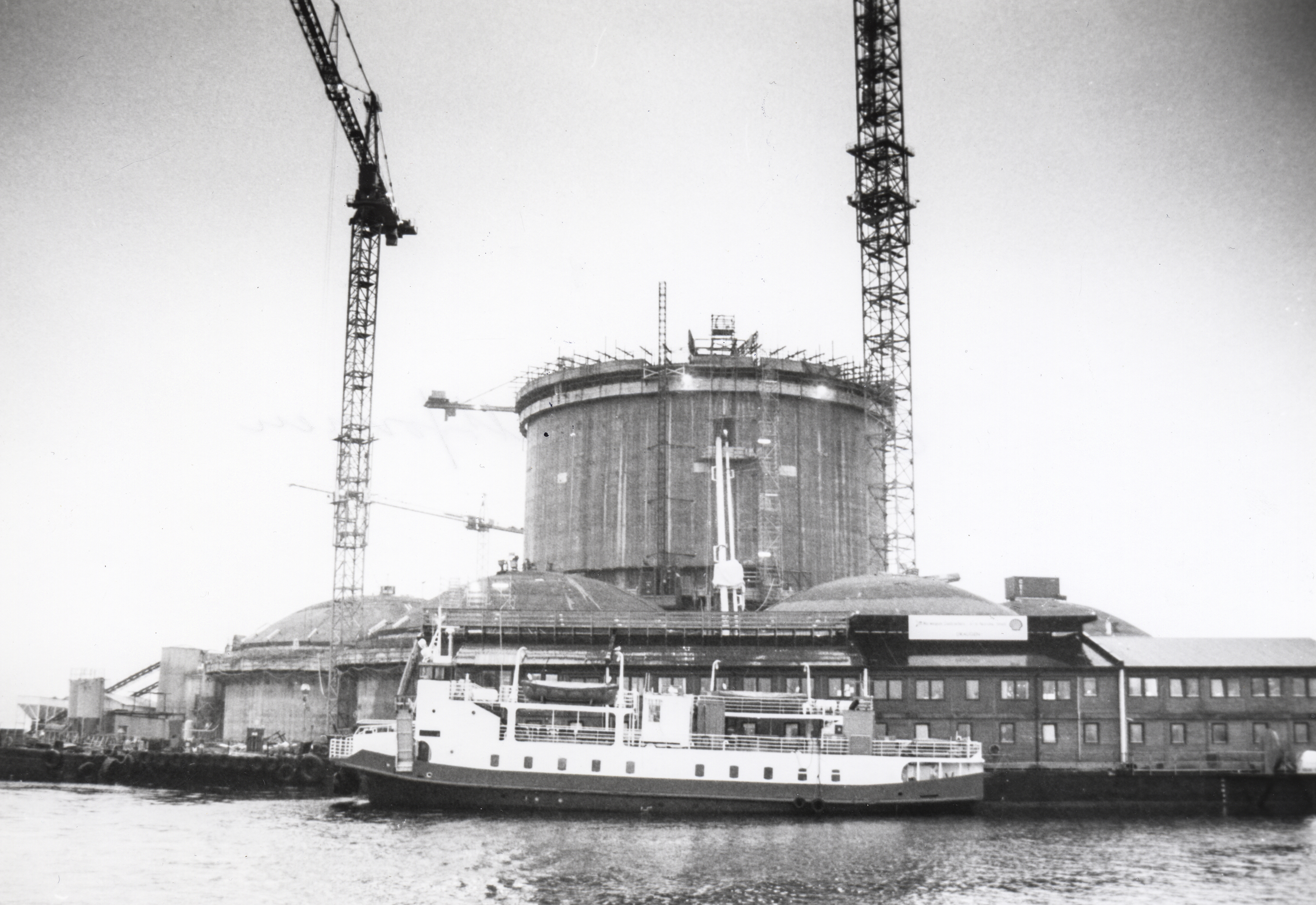
Shell wanted to try to avoid NC – the sole supplier of concrete GBSs to date – being its only option. An attempt was therefore made to create competition.
Peconor, a group comprising several companies including Sweden’s Skanska, was accordingly invited to submit a bid for building the structure.
The original version was presented, but the consortium was challenged to come up with an optimised design (as NC had already done). It transpired that the final bid from NC was far below the Peconor offer, allowing the former to retain its monopoly of building large concrete platform support structures.
The concept of a monotower GBS was not entirely new. It had been proposed as early as 1975 for Norway’s Heimdal field in the North Sea,[4] which was eventually developed with a jacket solution.
Once the PDO had been submitted, work began on optimising the GBS. This found that cylindrical components could be built with larger diameters. The earlier view had been that such shell structures could not have a diameter above about 30 metres. Any increase meant it would be unable to float on the shaft alone while building lower storage cells with sufficient volume.
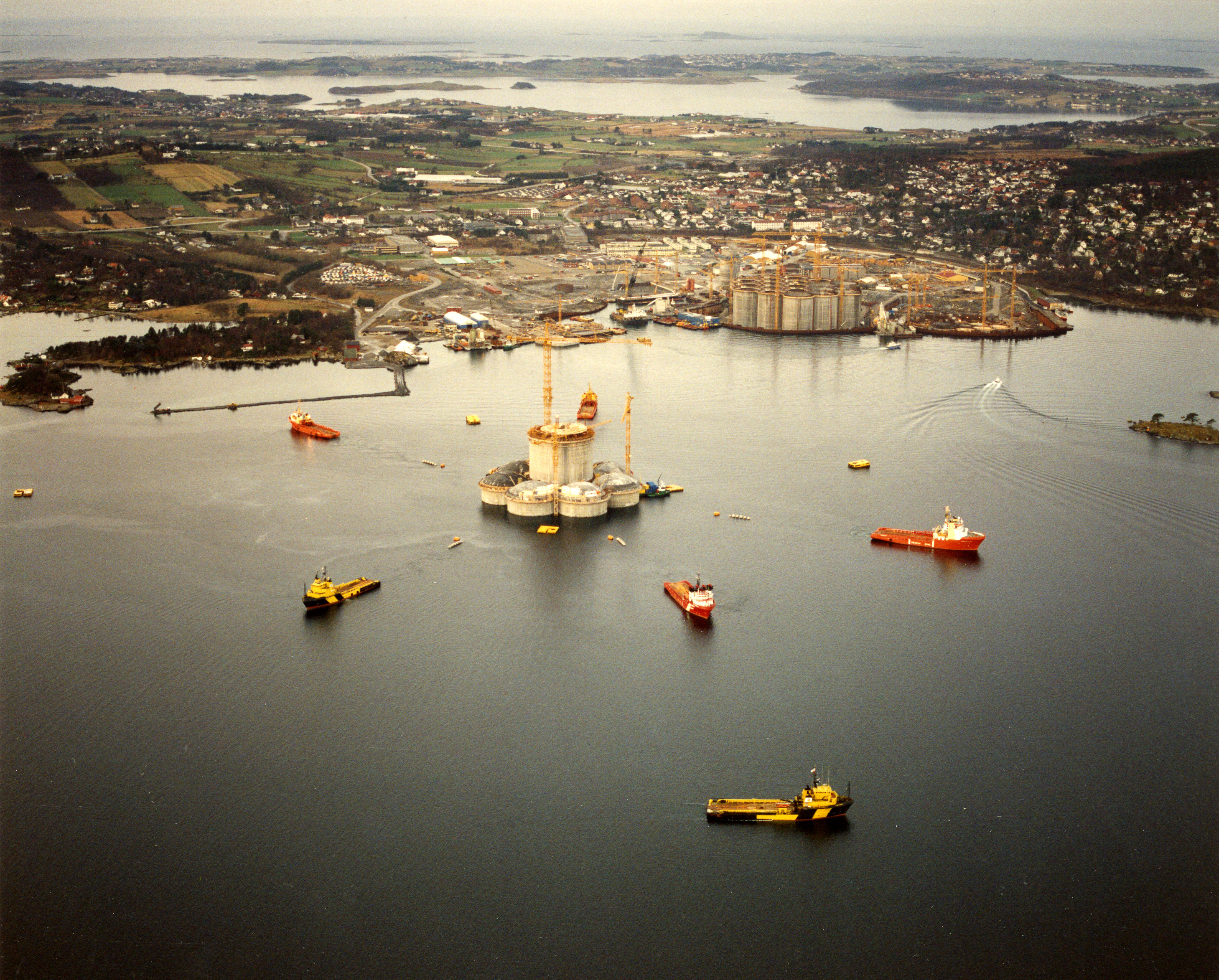
In addition, the length of the skirt piles (the part of the GBS which would penetrate into the seabed) was increased in order to improve the structure’s resistance to wave motion (see separate article).
So the big monotower provided the buoyancy needed by the platform at tow-out to the field while consuming considerably less concrete in terms of both volume and weight.
Another advantage was that the water depth along the tow-out route was very favourable in relation to the GBS height, allowing a relatively low freeboard during the operation. That ensured good stability and safety.[REMOVE]Fotnote: Steen, &. (2002). Den frie tanke : Om kreativ frihet og en ledende norsk ingeniør. Lillestrøm: Byggenæringens forl.: 110-112.
Boycott which backfiredLaying the ghosts