The Sleipner sinking and Draugen

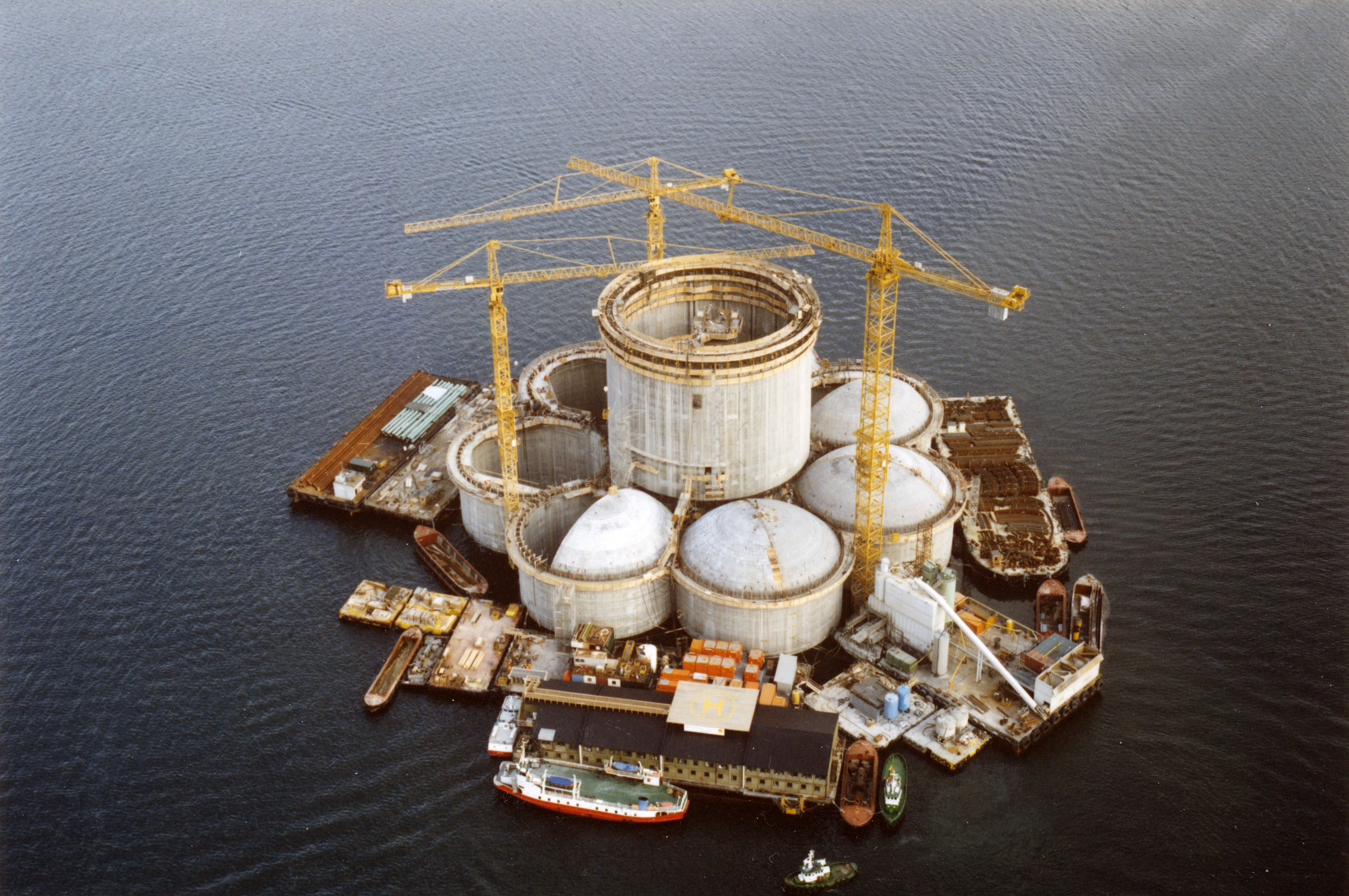
Construction of the Draugen platform was in full swing at this time. The immediate question was whether the same fate could befall its GBS.
Was there a weakness in the Condeep design which had so far gone undetected or failed to show up, or was this unknown fault confined to the Sleipner A structure?
The sinking was heralded at 05.49 with a loud report from inside the GBS, followed by two smaller bangs, and a substantial leak was immediately registered.
Continuous measurement by the control room established that almost 1 000 tonnes of water per minute were flowing into the drilling shaft.
The ballast pumps were immediately started, but the was much greater than they were designed to handle. About 18 minutes later, the GBS went to the bottom. That was long enough for the 22 people on board to escape without injury.
On its way down, the GBS imploded and all air in the storage cells was expelled. That created a tsunami effect so powerful that two tugs lying close to the structure lost sight of each other.
Sleipner A hit the seabed with great force in just under 200 metres of water.[REMOVE]Fotnote: Intervju med Einar Wolff, NCs prosjektdirektør for Draugen. Tremors from this impact were measured by several seismological stations (figure 2).
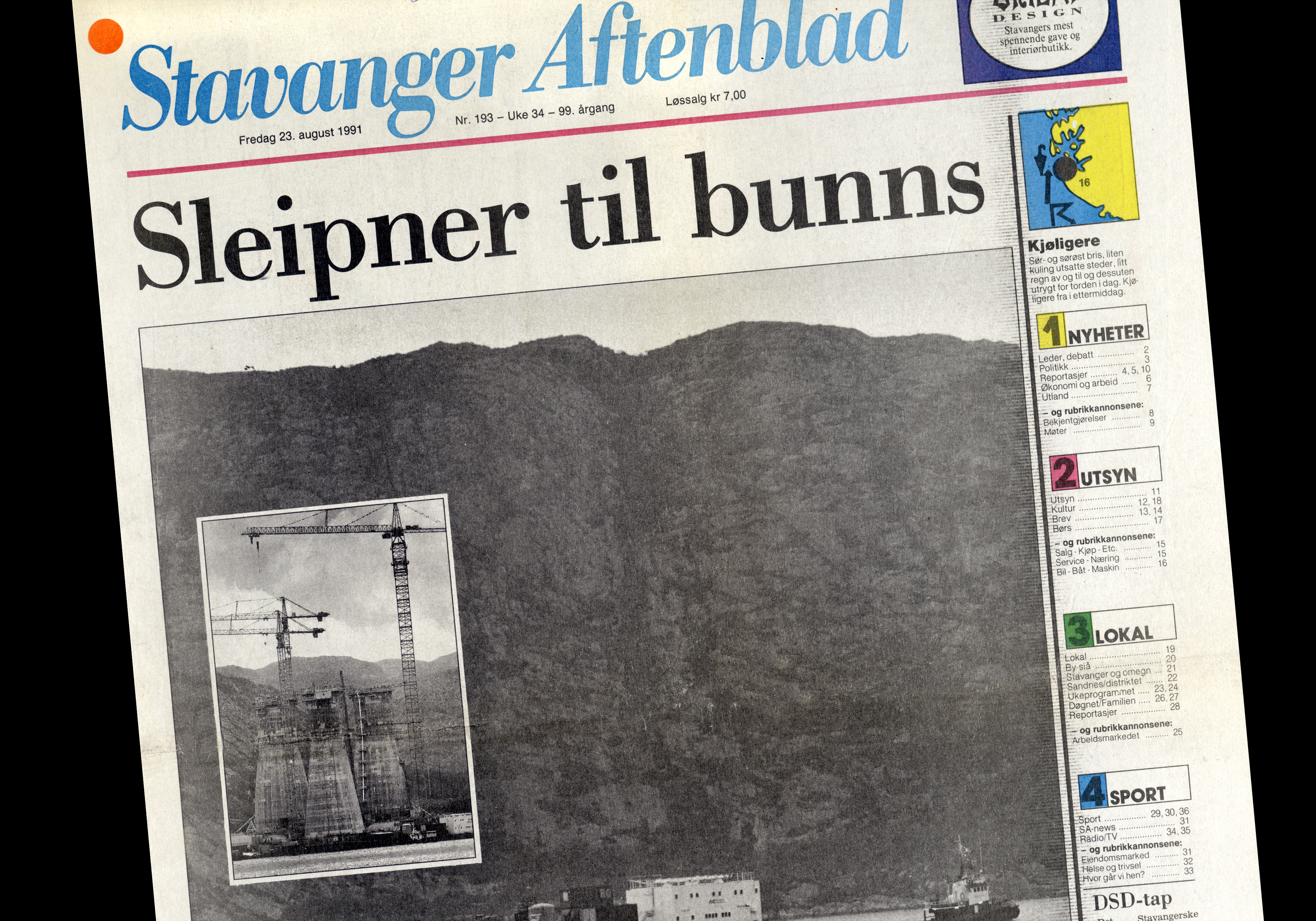
An investigation of the remains revealed that the GBS was completely destroyed, with remains scattered over a wide area in 170-220 metres of water.
Appointed almost immediately after the incident, a commission of inquiry led by operator Statoil sought to identify the cause of the sinking.
Builder Norwegian Contractors (NC) also established an internal investigation, which reached the same main conclusion as the other group.
This was that the concrete wall fractured because the connection points between the cells – known as the tricell (figure 3) – had been insufficiently dimensioned.
That in turn reflected errors which had arisen in the finite element analysis of the structural strength of the GBS.
NC commissioned a full-scale model trial which checked eight test sections. This work confirmed the causes identified by the engineers.[REMOVE]Fotnote: Steen, &., & Norwegian Contractors. (1993). På dypt vann : Norwegian Contractors 1973-1993. Oslo: [Norwegian Contractors].
The Sleipner GBS sinking also touched off a small earthquake at Shell, but actually had few consequences financially or in terms of progress.
As early as the day of the incident, NC representatives visited Shell’s offices to explain that it was probably caused by under-dimensioning of tricells.
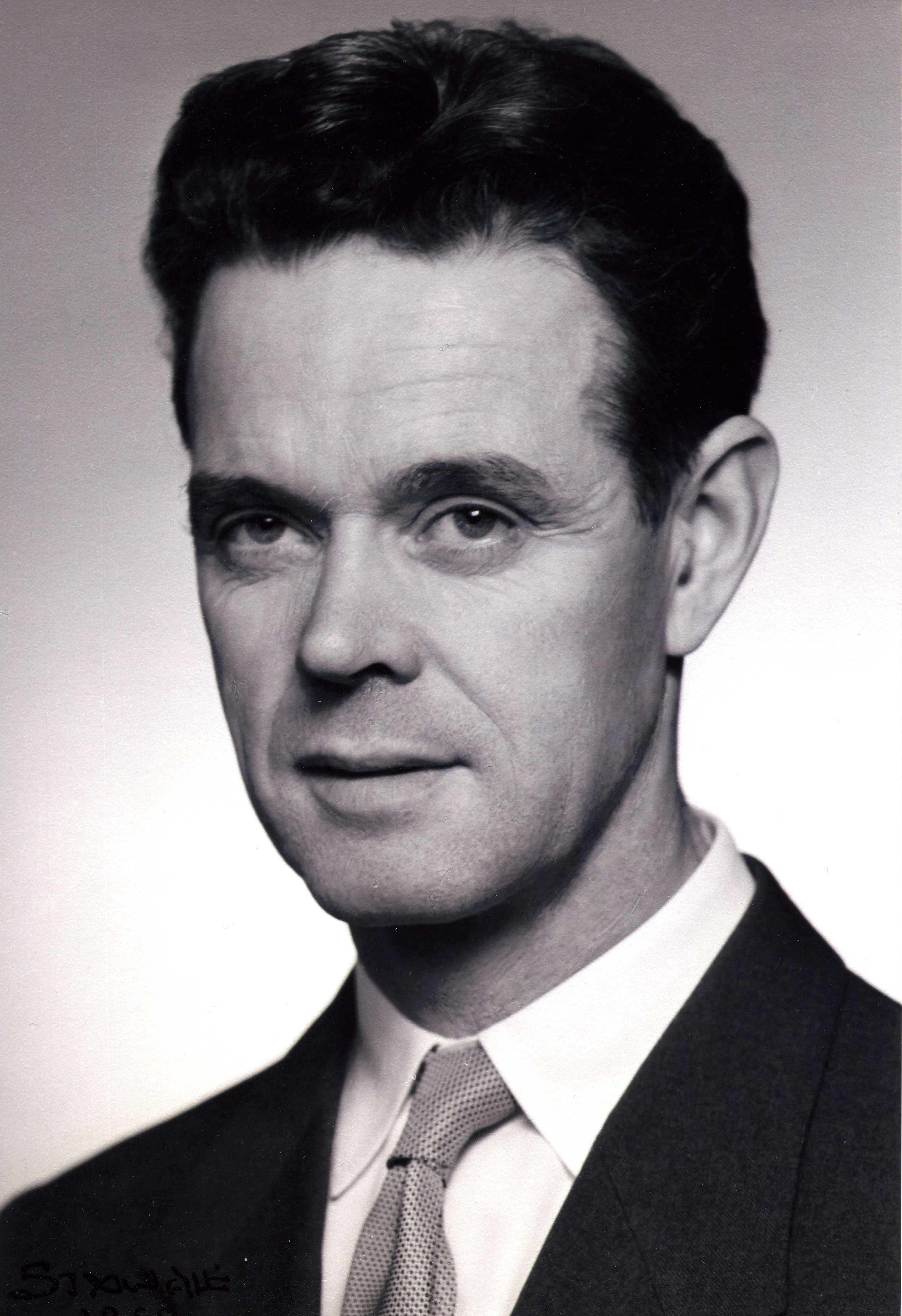
That in turn reflected inaccurate use of computer programmes at consultant Olav Olsen. Worse – the same error had been made on the Draugen GBS.
The news came as a powerful blow to Sigbjørn Egeland, Shell’s lead manager for construction of the Draugen GBS. “Until then, I’d had boundless confidence in NC,” he says.[REMOVE]Fotnote: Intervju med Sigbjørn Egeland, Shells hovedansvarlig for betongunderstellet til Draugen.
Shell initiated independent analyses, both in-house and externally, while work on the GBS was put on hold until the results were available.
After about three months, Shell got the same answers NC had obtained through its model trials and the construction process could be resumed.
As a result, the impact of the sinking was limited. The really significantly financial consequences arose from the ringing problem (see separate article).
“The principal effect of the Sleipner incident was that I lost a lot of my confidence in the supplier,” recalls Egeland. “From then on, it became necessary to test all the important conclusions with independent experts.”
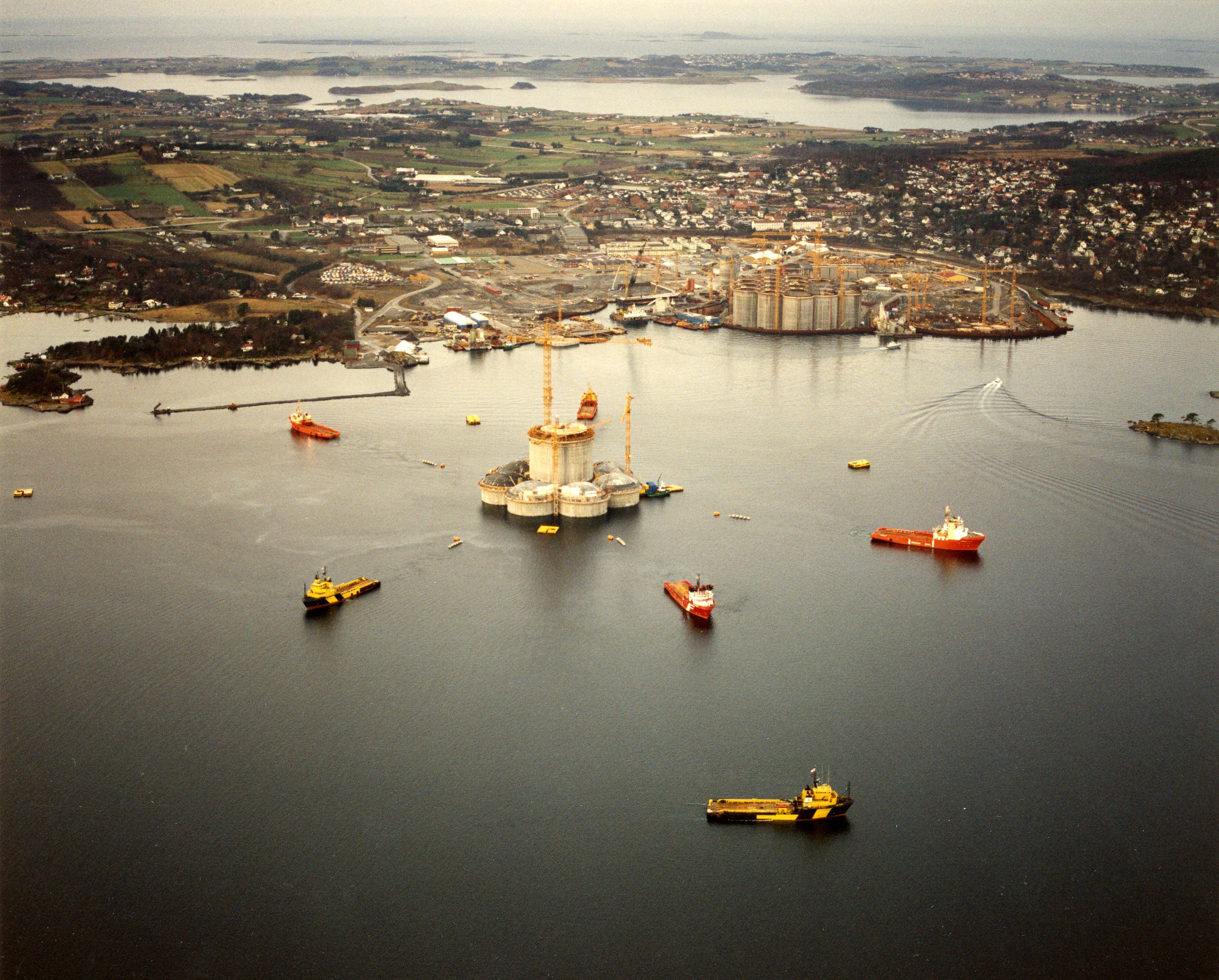